Asset inspection indoors and in confined spaces comes with its difficulties, whether you are using an indoor drone or more traditional methods like scaffolding and climbing.
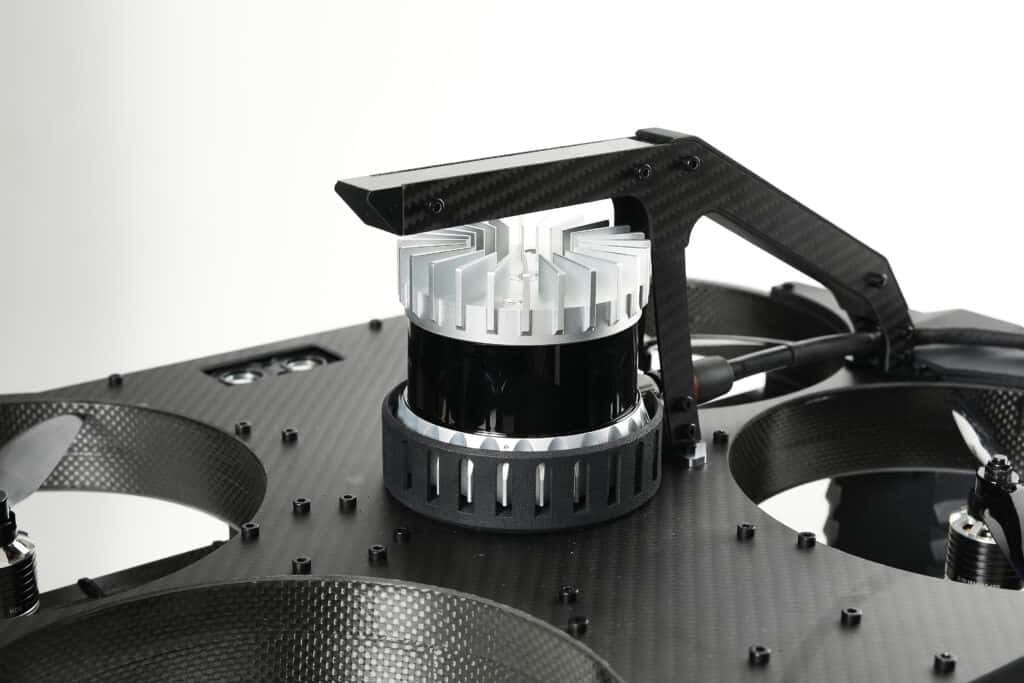
A 3D scanning LiDAR of the type discussed in this article is mounted on the Scout137 Drone System.
Dangerous atmospheres, hazardous access, heights, fluids, debris and lack of ambient light create serious safety concerns when working in indoor industrial spaces. Drones and other tech-assisted inspection methods help minimise the risk, but present problems related to navigation, position and stability especially for non-entry or beyond line-of-sight (BVLOS) operations.
Inside a large steel structure, navigation based on GPS and magnetic compasses are in most cases rendered useless. In such cases, relying on only a video camera feed for navigation is far from optimal.
An indoor drone equipped with 3D LiDAR scanning technology instead of GPS makes all the difference for such inspection jobs.
What is LiDAR?
Light Detection and Ranging (LiDAR) is a remote sensing technology that uses pulsed laser light to measure physical distance. In short, it rapidly fires laser beams and measures the time it takes for emitted light to travel to the nearest surface and back.
3D LiDAR scanning technology has been used in industrial applications for years, in everything from agriculture and aviation to geosciences, to measure precise information about the physical world.
Not to mention cars: The automotive future is all about self-driving. Billions of dollars are invested into the development of autonomous driving. A key question is whether it can be achieved with or without LiDAR sensors. Tesla, with their great market share, are betting on combining regular camera technology with Machine Learning: An enormous amount of collected data enables the use of cheap cameras instead of LiDAR for this task. More basic driver-assist functions are covered by radar or ultrasound sensors.
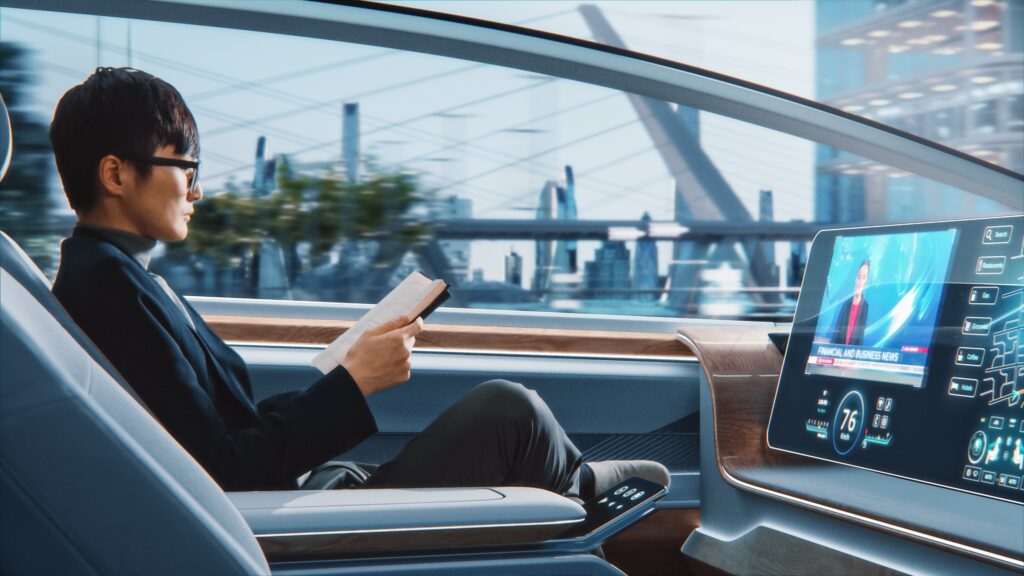
On the other hand, Chinese automotive company Xpeng invest heavily on LiDAR technology and plan to use LiDAR as part of their sensor package for autonomous driving. They believe cameras alone will not be enough.
Something that cannot be covered by using camera-based navigation is the absolute lack of ambient light. Storage tanks, silos, maritime cargo rooms etc. are often pitch black on the inside, very self-similar and represent volumes too large to light up all at once. Here, the use of conventional cameras for navigation becomes difficult and less robust.
But the LiDAR sees also in absolute darkness, with good range and great accuracy.
Using proven 3D LiDAR technology together with our advanced software, we have created a synthetic GPS system. Just as with a GPS drone, the operator can fly in ‘position mode’ supported by 3D LiDAR data. This keeps the drone in place and ensures anti-collision, while the operator focuses on the images.
Nicolai Husteli, CEO ScoutDI
The OS series of sensors from Ouster are very good for indoor industrial spaces. They are lightweight which allows them to be carried by a drone, they have good range, provide the centimeter accuracy needed for its inspection purposes and come at a reasonable cost.
We chose these 3D LiDAR sensors because of the ideal compromise of properties and value for money. They can also be used for capturing mapping data about complex environments such as forests and building interiors. But for us, the sensors let the drone see what you cannot see.
Overcoming indoor navigation problems
3D LiDAR mapping has been a fundamental building block for our inspection technology for years and is built in to the indoor drone Scout 137, which hit the market in 2020. Thanks to its (pat. pending) combination of 3D LiDAR sensor, vertical laser sensors and a powerful onboard computer, the Scout 137 indoor drone knows where it is at all times. Adding precise situational awareness increases safety and gives greater confidence in the results of an asset inspection procedure.
This remains true regardless of lighting conditions. With 3D LiDAR, no ambient light is needed for navigation, so inspections can be conducted with confidence even in complete darkness. Of course, light is required to generate useful visual inspection data. But it is only required locally – you only need to light up what’s directly in front of your inspection camera.
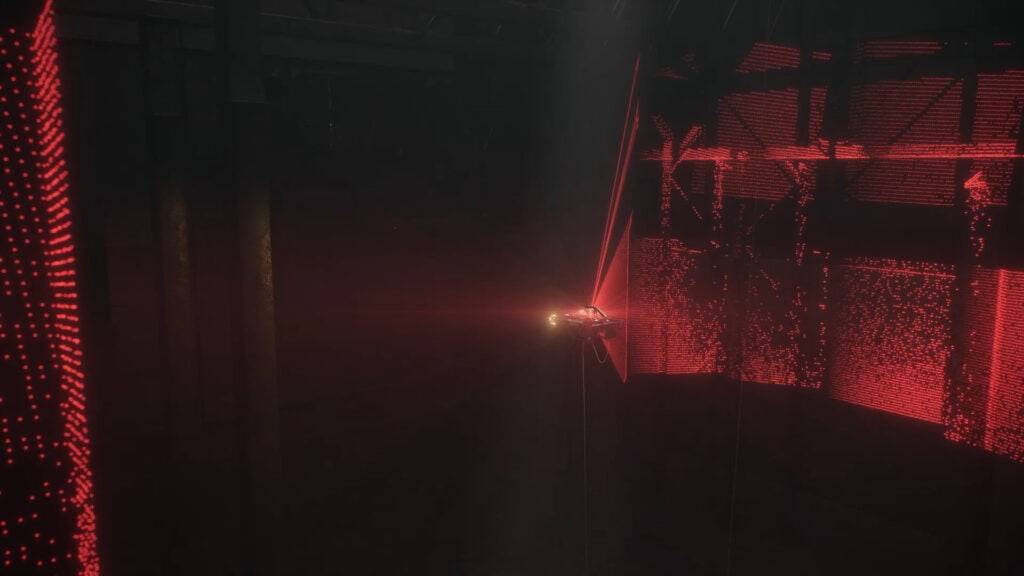
Benefits of LiDAR for the drone pilot
If the drone pilot doesn’t know what is next to or behind the drone, the inspection process can be impacted by confusion and lack of overview. This poses a direct safety threat, threatens the integrity of data quality and coverage, and risks damage to the asset and the drone itself.
So while GPS navigation isn’t feasible indoors, a LiDAR-enabled system is an ideal option. LiDAR provides situational awareness to the drone pilot. It allows the pilot a mental image of the situation inside the volume where the drone is operating – even in a non-entry or beyond-visual-line-of-sight (BVLOS) situation. It also provides data to the drone’s autonomy computer so it can keep itself stable avoid obstacles and maintain position.
“Using proven 3D LiDAR technology together with our advanced software, we have created a synthetic GPS system. Just as with a GPS drone, the pilot can fly in ‘position mode’ supported by 3D LiDAR data. This keeps the drone in place and ensures anti-collision, while the pilot focuses on the images”, explains ScoutDI CEO Nicolai Husteli.
The Scout 137 is tethered with a lightweight cable to a ground station. All the data is available in real-time via the robust, high-speed data link to the operator using the Scout tablet. The operator sees the live camera feed on-screen with the 3D map generated by the LiDAR, giving a comprehensive overview of the inspection target in real-time.

The 3D map can be zoomed, panned or rotated to whatever angle will provide the best insights for drone operations. You can also of course explore and interpret the data after the inspection has finished.
Connecting the ground station to the internet allows remote participants to join a live-streamed inspection and see the same visual and 3D LiDAR data in real-time via the Scout Portal, that the operator sees on his tablet.
Location-tagged inspection data
In the case of ScoutDI’s indoor drone technology, the 3D LiDAR mapping is working in real time and therefore serves the pilot and the drone well during the live inspection job.
But that’s not all. All inspection data (video and still images), is location-tagged on-the-fly with the drone’s exact position and heading inside the inspection volume. In addition, whenever the pilot sees something interesting, a dedicated controller button can be clicked to add a finding, or a point of interest (POI). This can be a patch of corrosion, a beginning crack or anything interesting that’s worth checking on later.
When reviewing the inspection data, the flight path is shown on-screen with a string of little red triangles marking the findings that were added. This makes them easy to find in order to have a closer look, add annotations and generate a report. Having the exact position and heading of the drone at that point, you also know how to locate the finding inside the real asset!
So 3D LiDAR data helps the indoor drone user in real-time and in post during data review. But it also helps you overcome the problem of not knowing what you don’t know.
Have confidence in data coverage
How does an indoor drone pilot know with confidence that the job is done – that 100% of the infrastructure has been inspected? This is a tough challenge in big, closed spaces with repeating, self-like structures where everything looks the same. Another benefit of the Scout 137 is that the flight path of the drone is recorded together with the 3D map generated from the 3D LiDAR scans during the inspection.
So the drone operator knows with confidence when the inspection is complete and can demonstrate this to any stakeholders.
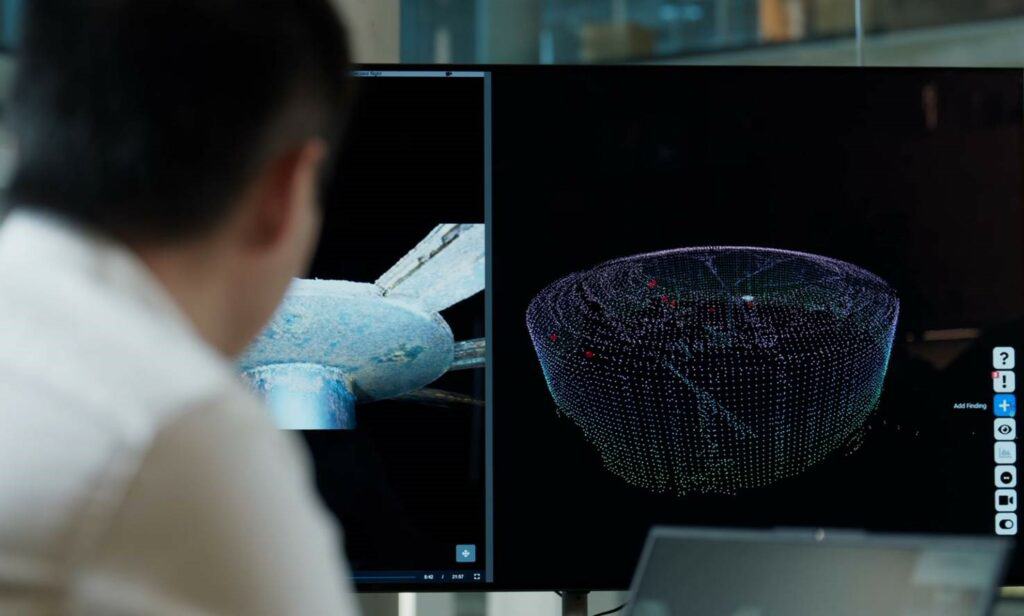
LiDAR improves asset inspections now and in the future
Not only does this give the operator confidence in the completion of a full inspection, it also increases the speed of the activity, reducing asset downtime and thus overall cost. The live-streaming capabilities support remote inspection, which offers yet more cost and efficiency benefits.
The results generated by the 3D LiDAR technology also help maintenance engineers to better plan future inspections since both visual and 3D data will be available for the inspection planning process.
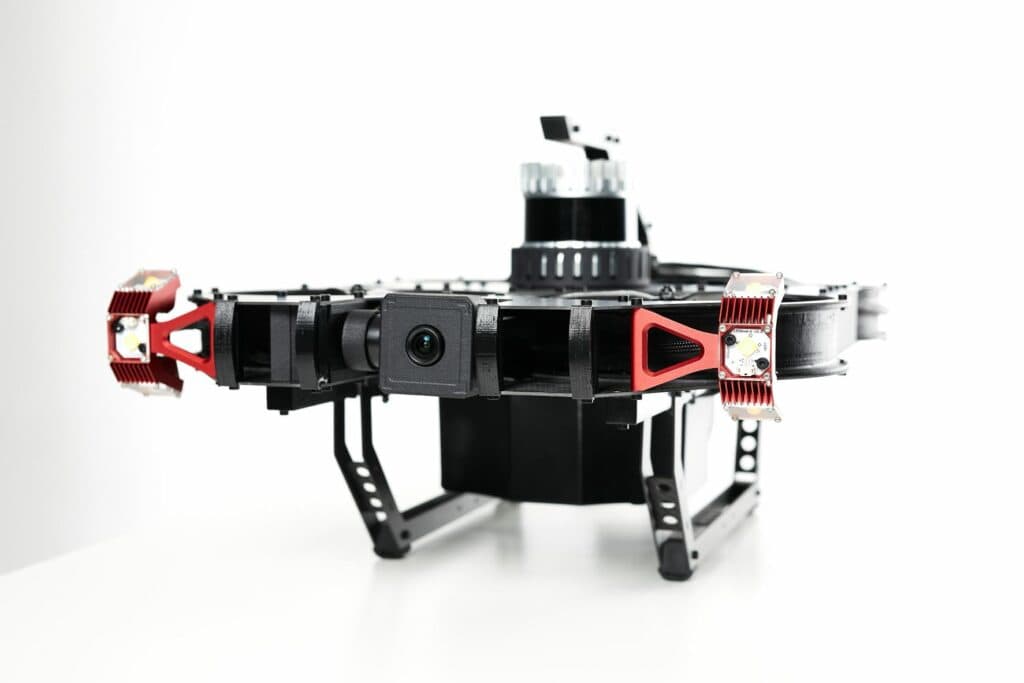
Speaking of the future, a solid autonomy platform with a fully integrated 3D LiDAR sensor at it’s core is a great starting point for further autonomy to be added. So that, in addition to be able to confirm the inspection path in post, you might also be able to program the path in advance. This would reduce the job to 3 main points: Deploy indoor drone, start the inspection program, extract indoor drone.
ScoutDI’s team has deep competence within robotics, autonomy and computer vision, as demonstrated for example in the REDHUS and ADRASSO research projects together with DNV. We also have a patent pending for the way 3D LiDAR data is being used for positioning and navigation plus location-tagging of inspection data. Leadership in these disciplines and a head start integrating 3D LiDAR in an indoor drone system, is an excellent position when it comes to implementing the type of scenario mentioned above and making it a reality in the industry.
Find out more about the capabilities of 3D LiDAR and the Scout 137 asset inspection drone by watching this free on-demand webinar.
Read more about the ADRASSO project here.
ScoutDI employ industry leaders in computer vision and autonomy. Read more about this here.
Read more about life as an autonomy engineer in ScoutDI, here.