Enabling stress-free drone-based UT gauging
UTM Payload
The Scout 137 Drone is now an excellent collector of high-resolution visual data and UT measurement data. One drone, one flight, multimodal data
“If you can reduce or eliminate climbing from structural assessment jobs, great benefits in terms of safety, time and cost are unlocked.”
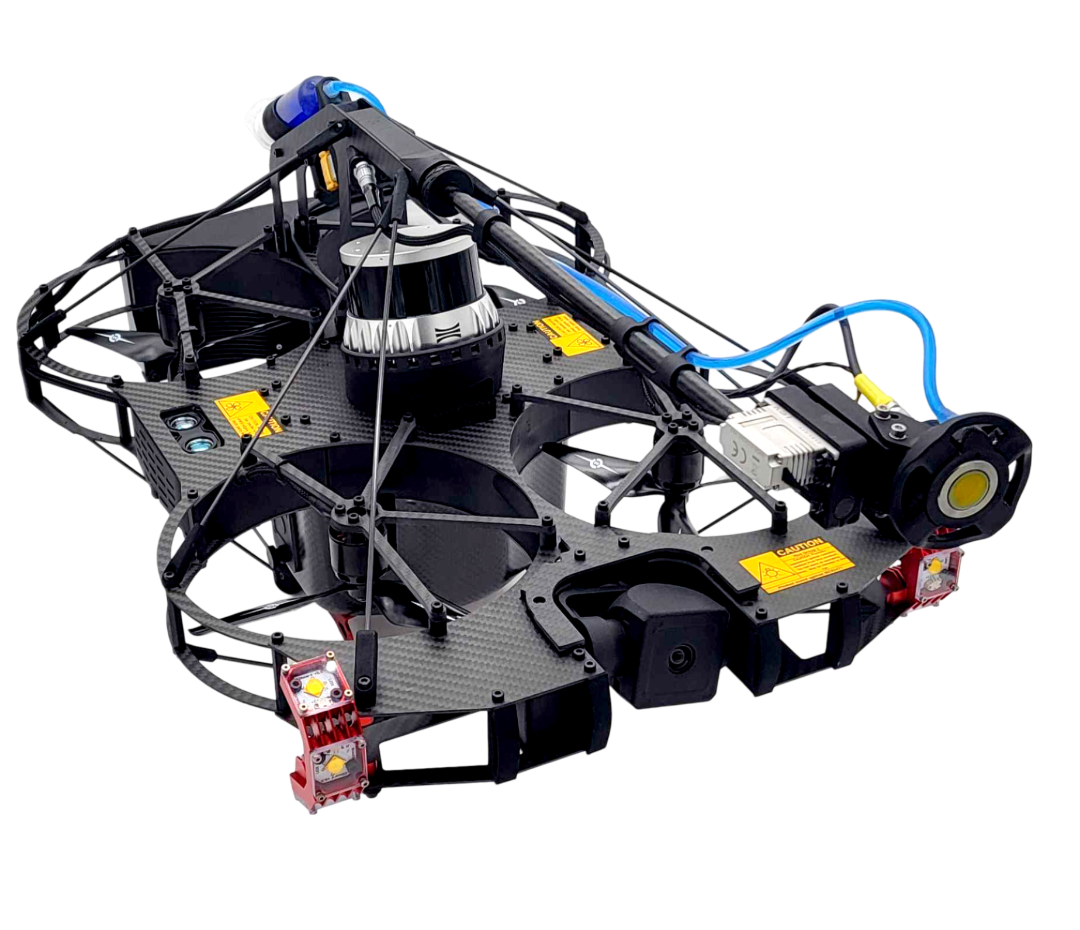
Safer Remote Inspections
Say hello to the UTM Payload
The UTM Payload adds Ultrasonic Thickness Measurements (UTM) with live A-scan to the inspection capabilities of our Confined-Space Inspection System. In the same flight.
Fully integrated with our Scout 137 Drone System and the Scout Portal, UT measurements are a natural addition to our end-to-end confined-space data solution.
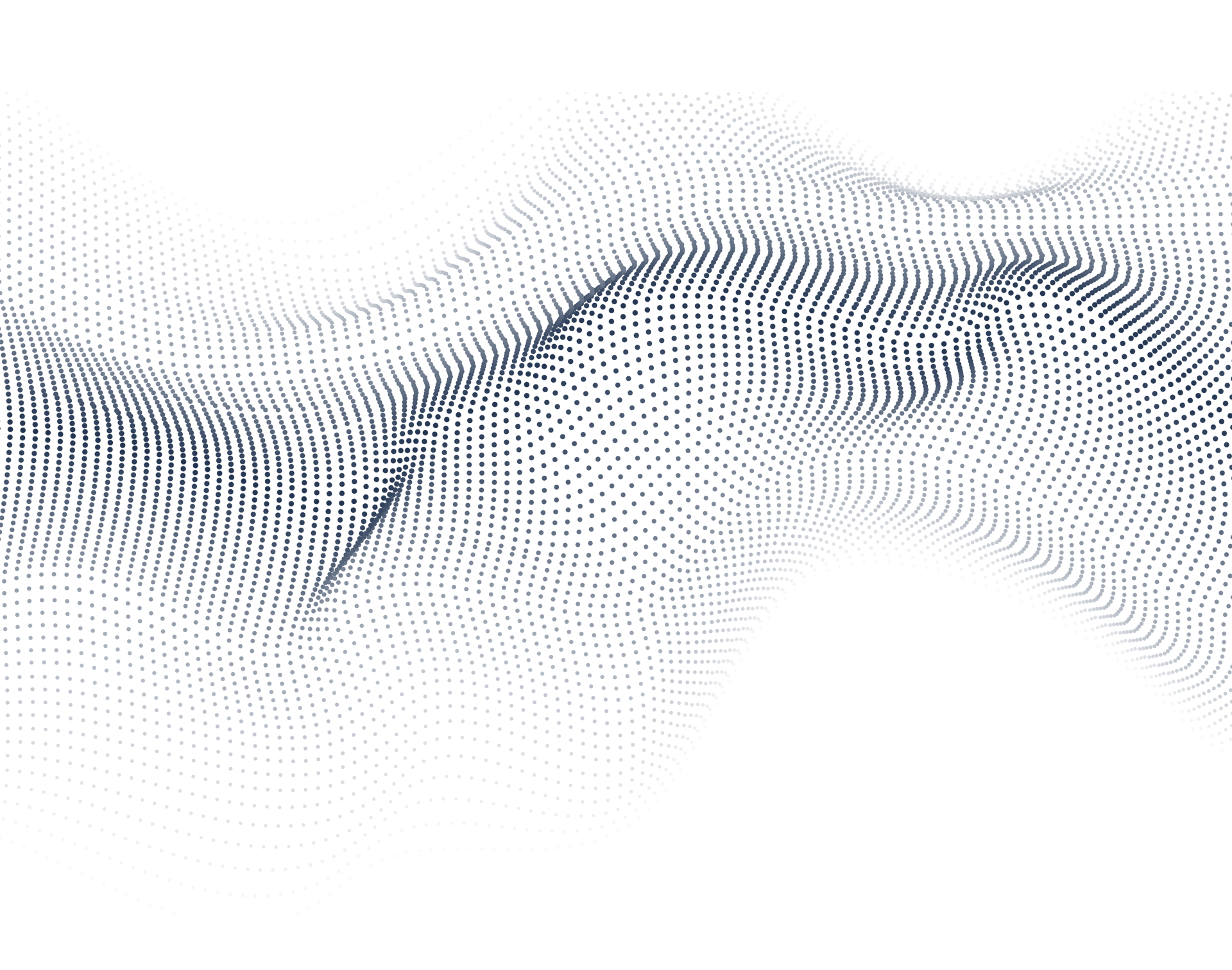
Unlimited flight-time for stress-free UT inspection
Anti-collision, BVLOS support and location-tagged data

Live A-scan for on-screen UTM evaluation as you fly

Motorized UT probe head, remote adjustment and smart release
Unlimited flight-time for stress-free UT inspection
NDT and specifically UT testing with drones in large volumes is risky and time-consuming work. The drone may be high up and far away, barely visible behind structure or even completely BVLOS (Beyond Visual Line of Sight). There is a lot to think about and external distractions are unwelcome.
The unique tethered design of the Scout 137 Drone System provides unlimited flight time, allowing you the time needed to perform risky contact operations remotely. No need to worry about batteries. No need to stress. Take your time and do it right.
← Click the player for UTM Payload intro video.

Remote, location-tagged UTM with live A-Scan
UT measurements start automatically upon surface contact and live A-scans can be frozen for easy evaluation. Zoom/drag to look at range & gain, and evaluate the waveform before saving the measurement.
3D LiDAR ensures safe automatic anti-collision, rock-steady positioning and visual navigation support, effective also in BVLOS conditions. Camera feed, minimap and the probe-head laser help guide you safely through the contact phase towards successful measurements. All your visual data and UT measurements are automatically location-tagged.

Motorized adjustable UT probe arm with smart release
The UT probe is mounted on a custom-designed probe arm (pat. pending). The flexible head mount allows just enough play that surface contact is easier to establish.
Permanent magnets around the probe face helps maintain the contact on magnetic surfaces. The motorized probe head has a Smart Release function, which disconnects the probe at the click of a button and without moving the entire drone body.
The probe head angle can be adjusted remotely while flying, so you can measure surfaces with different orientations in the same flight.
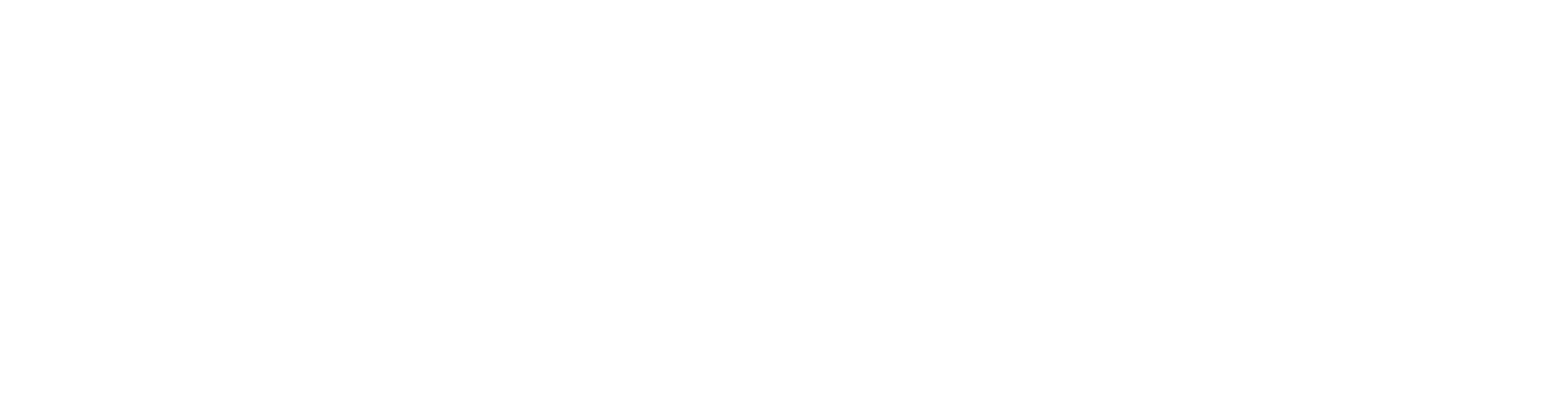
IACS-compliant UT probe for class surveys
Developed in collaboration with Tritex NDT, the UTM Payload features a robust, single-crystal multiple-echo UT probe for precise measurements. It is the same technology as utilized in their popular Multigauge 6000 UT gauge. This UT probe technology is widely endorsed for its robustness and compliant with the IACS special equipment requirements for thickness measurements on ships or mobile offshore units.
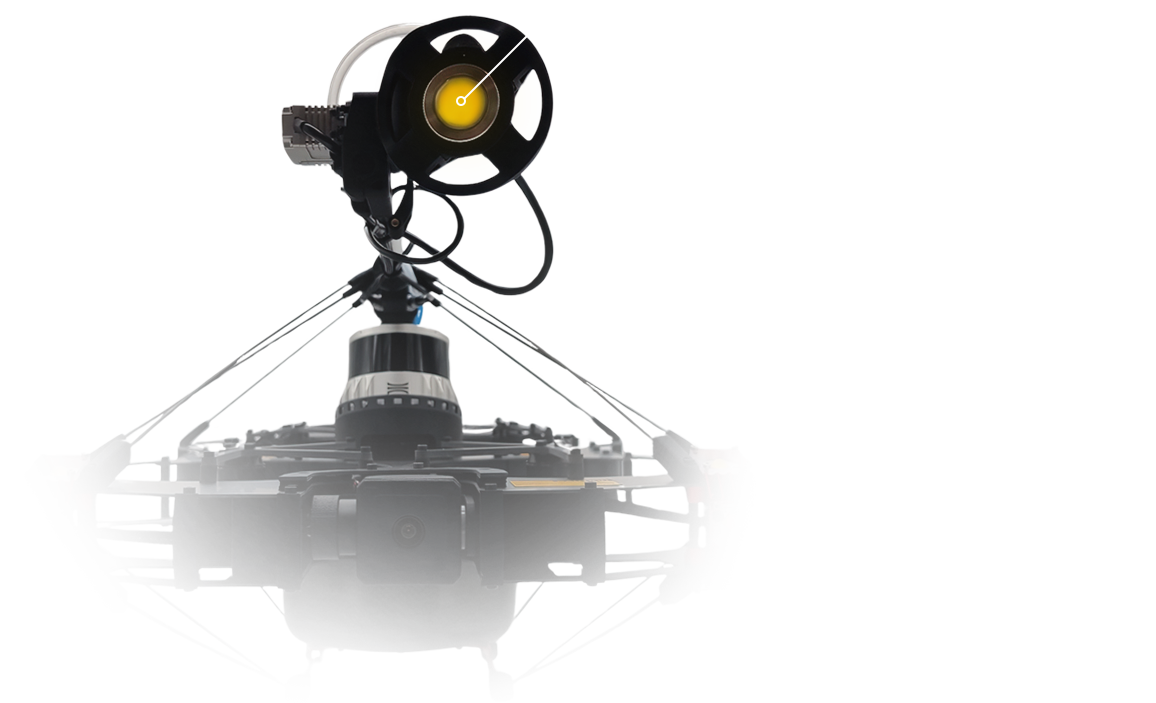
Frequency | 2.25 MHz | 3.5 MHz | 5 MHz |
Measuring Range | 3–250 mm (0.120" to 10") | 2–150 mm (0.080" to 6") | 1–50 mm (0.040" to 2") |
Color | Yellow | Green | Blue |
Diameters Available | 13 mm (0.5") | 13 mm (0.5") | 13 mm (0.5") |
Suitable for | Most UT gauging applications. Works well on heavy corrosion. | For UT thickness measurements on thin metal which is corroded. Normally used only if measuring down to 2 mm is of importance. | Ideal for UT gauging on thin metal in good condition. Not advisable to use as the main UT probe. |
Three frequency options and replaceable UT probe membranes
Frequency options, 2.25 MHz, 3.5 MHz and 5 MHz are available for the UT probe, offering versatility across applications, as specified in the above table. The 2.25 MHz UT probe option is standard for the UTM Payload, covering a range of metal thicknesses and conditions.
As UTM probes are routinely dragged across rough and dirty surfaces they eventually become scratched and worn. As with the Tritex UT gauges, replacement membranes are available to prolong active lifecycle and ensure job completion!
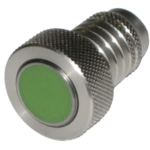
3,5 MHz
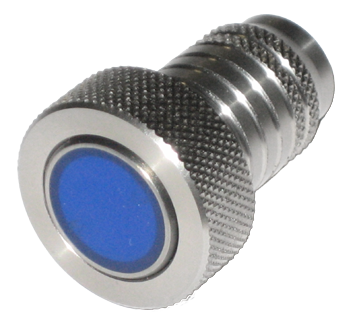
5 MHz
Generous couplant container and Rapid Refill
The couplant gel container has capacity for up to 100 clicks on the gel button. Exactly how much UT testing you can do per container, depends on the condition of the surface and your preferences while probing.
The couplant gel pump is controlled via a dedicated on-screen button in the Scout App. When more couplant is needed, it’s easy to swap containers and refill an empty one.
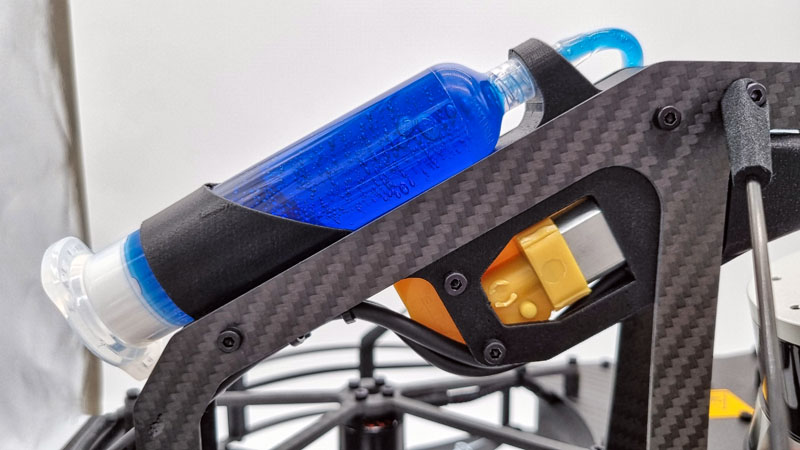
Data integration to the Scout Portal
All UT data and visual data is integrated in the Scout Portal. The Scout Portal has built-in SLAM and generates a 3D-visualization of both datasets in the assets, based on their location tags.
This means that you can compare 4K photos and UT measurements from the same flight session, along the same flight path, and correlate your findings. The inspection is easily shared to external stakeholders, for quicker and more informed decision-making.