In order to ensure the safety and integrity of industrial assets, inspection technology must consist of two key parts:
Data acquisition. The right data needs to be collected with sufficient coverage and precision.
Data science. How can we turn large amounts of data into insights and useful information?
For too long, equipment manufacturer focus has remained on the data acquisition side, leaving the part where data is made useful and manageable an open-ended story after the last photo is saved to the memory card. Gigabytes are not useful in themselves unless they’re well organized and presented.
But how data-savvy is the industry? Are we interested in data for the right reasons, and can we accommodate data sharing and data usage on a larger scale? Why does data-savvy still live in the meeting rooms in some industries?
Digital collaboration trends
Digital twins and asset management systems seem to be in high regard in many heavy industries.
A digital twin is a virtual representation of a physical asset that allows for real-time monitoring and analysis of its performance, predicting potential problems and optimizing operations.
An asset integrity management system (AIMS) is a process framework often implemented as a software application helping organizations manage their physical assets to ensure safe and reliable operation over their lifecycle, while minimizing risk of unplanned outages, accidents, and environmental incidents.
Clearly, there is a digitalization interest, but it still seems viable mainly in large, high-revenue companies. There must be reasons why digitalization is not more prolifically present in the heavy industries.
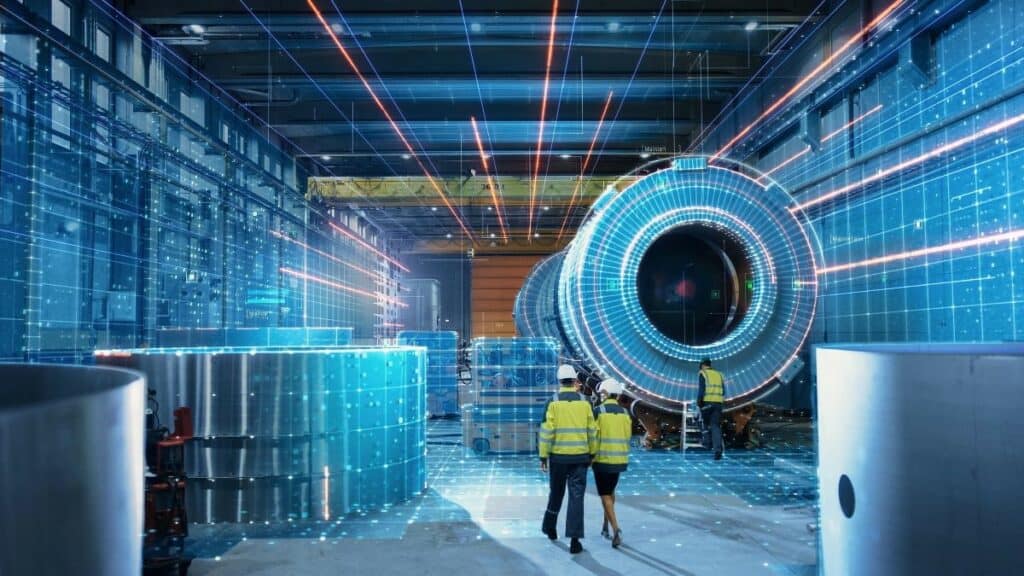
How to deal with common digitalization challenges
So, what’s the problem? Can’t we just get on with it already?
As many heavy industries are traditionally operated with a focus on manual tasks and procedures, implementing digital solutions is challenging. Training and re-staffing is difficult and expensive to do while also maintaining operation.
But the elephant in the room regarding digitalization of heavy industries, is probably integrating legacy systems and equipment with new digital technologies. Many industrial facilities have been in operation for decades and have a mix of old and new equipment, making it difficult to integrate new digital solutions.
The lack of standardization technology protocols and data formats is also a prominent issue. Communication between systems, and data “recycling”, I.e., repurposing data for use outside its original intention, becomes challenging. Then there’s data security. But of course, such problems only enter the scene once you have the data.
And in many cases, there is not enough data.
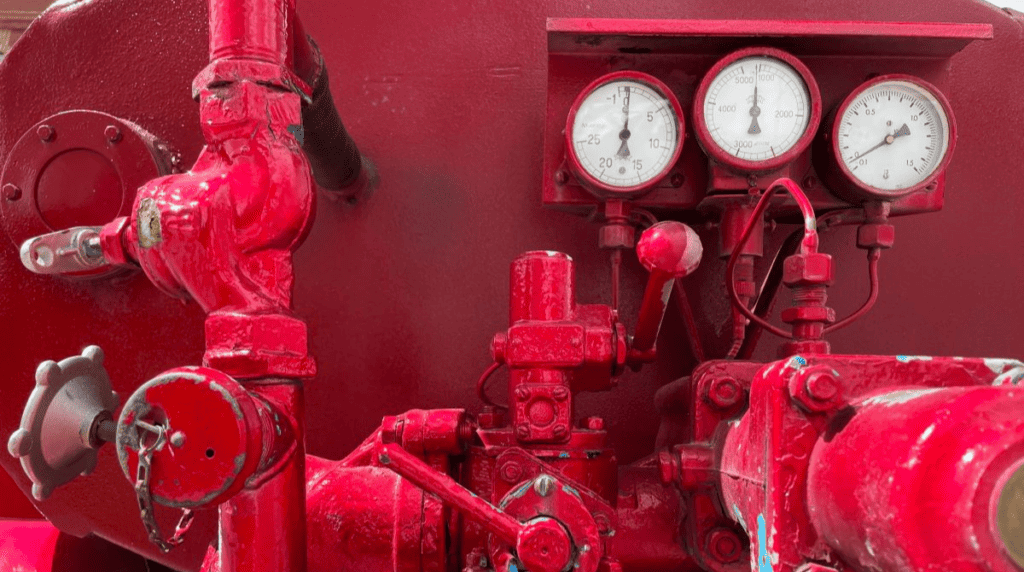
Get more data
If you want data, have not been generating enough data, or what you have is not fit for re-purposing, then you must start making data. If you have several assets, starting digitalization now could allow you to harvest great advantages in the future. But how?
Well, you can start by retrofitting digital interfaces and investing in robotics.
Creating your own data has several benefits. You can ensure that it is accurate, relevant, and up-to-date. You have control over data quality, privacy and security. And it most likely leads to better understanding of the data and its context, enabling more informed decision-making.
Relevant data is crucial for Machine Learning (ML) as it is the foundation upon which models are trained and evaluated. Garbage in leads to model overfitting or bias. The result is poor performance on new data, and thus marking an disappointingly early end to your digital transformation.
It is possible to carefully select and preprocess second-hand data, but there’s nothing like getting your own.
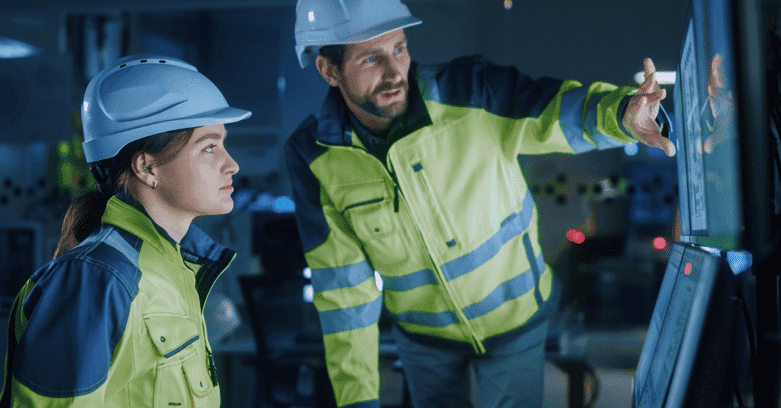
Connected sources and rich data
Controlling your own data harvest also puts you in a nice position to interconnect your data sources. Data from similar or identical assets can be combined to provide more comprehensive views of operations, not to mention statistics and prediction. It can potentially be equal to or better than having more data from the same source. If you collect and procure the data purposefully.
Connected sources pave the way for cross-referencing and enhanced cause-effect analysis, increased reliability and accuracy. It can uncover new insights and patterns that enable more proactive problem-solving and optimization of operations. In turn, this too helps reduce downtime and increase the lifespan of your assets.
Another trend we like is using rich data for interpretation and reporting in various industries. Rich data refers to data containing multiple forms of information which can be combined to provide a more comprehensive overview of the situation.
In our case, the 3D LiDAR sensor of the Scout 137 Drone System not only provides on-site situational awareness and positioning. It also provides location-tagging on all data presented in the Scout Portal.
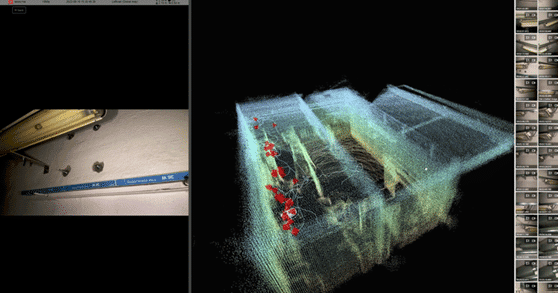
📢Watch this 4-minute video to learn more about the Scout Portal
The Scout Portal uses location-tagged video and photo to render a comprehensive overview of the asset and the inspection data. Using location-tagged data, the Scout Portal shows you the exact position from where each hi-res photo or second of video was shot. All these positions are rendered as a thin line in the point cloud, making it easy to confirm the flight path, and all POIs are marked as red objects that you can click to open the corresponding 4K photo. Quite far from just browsing bunch of folders full of photos!
Additionally, with the growing popularity of Machine Learning (ML) as mentioned above, these concepts are increasingly used to train and improve ML models, enabling more accurate predictions and insights.
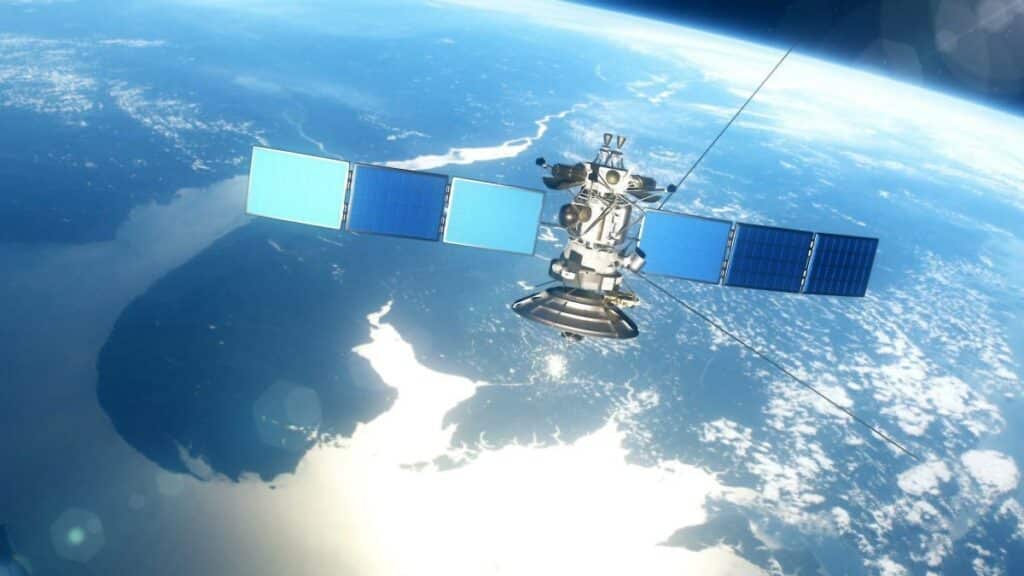
As the industry calls, the industry responds
As heavy industries call for solutions to unlock their data-driven futures, it is pleasing to see how other industries happen to be on the rise to close technological gaps in traditionally suffering sectors.
There is a wealth of new offerings in the SaaS world, process support tools, data integration services etc. And there are substantial changes ahead in data connectivity, storage, and accessibility.
This “new age” of data connectivity is characterized by the emergence of advanced technologies like StarLink Maritime, using a network of low-Earth orbit satellites to provide high-speed internet access even in offshore and maritime areas.
These industries can expect to see a significant improvement in their internet connectivity, which will benefit their operations and enable things like live remote inspection (live video streaming with 3D point-cloud data) as offered in the Scout Portal.
Still, it is important to note that low-bandwidth options will be necessary for many years to come.
This is especially important in developing countries or rural areas where infrastructure may not be as advanced, and of course in offshore and maritime.
So, in situations where high-bandwidth features are not viable, it is important to offer a functional alternative that still provides value.
The future of inspection technology
It has been a trend over some years now to use robotics to generate or acquire data.
Traditionally though, the role of the inspection robotics company has been to provide rich data, for example video, high-res photos plus some telemetry.
Taking it a step or two further, ScoutDI has been amongst the first in the industry to offer a drone inspection solution that is two-fold: A tethered drone system (1) that can be connected to a data management service via the internet (2).
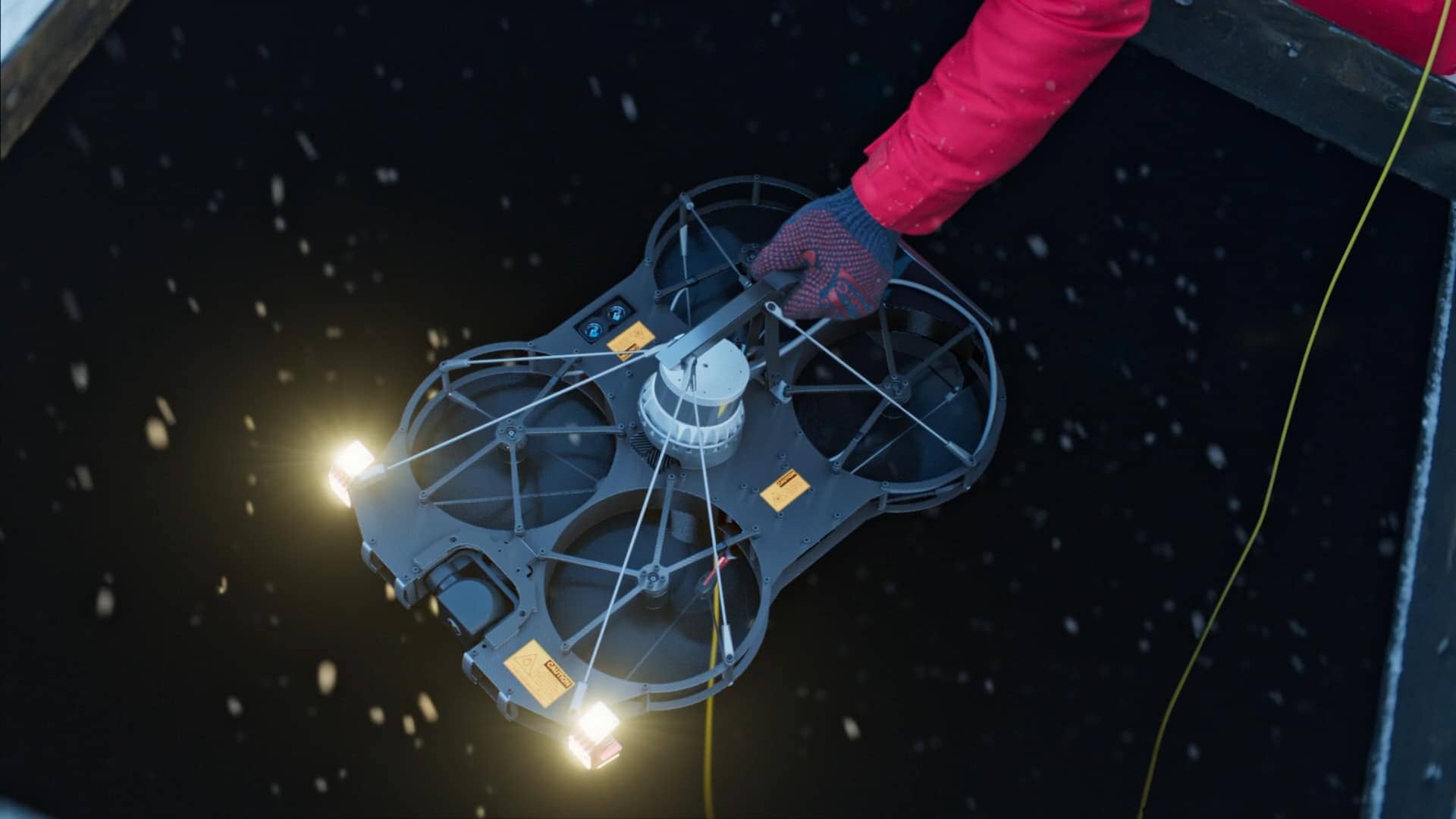
On one hand, we need to make the Scout137 Drone System as usable as possible in as many situations as possible: We must create a solution that promotes the safety and efficiency of the pilot and the on-site inspection crew and lets them focus on getting high-quality data and good coverage:
- coverage complete enough to verify the validity of the inspection, and
- high enough data quality to form the basis of decisions towards continued production and maintenance work.
On the other hand, we’re working hard to make this data easy to access, manage and become even more useful in the Scout Portal:
- The Scout Portal must enable easy access and sharing of all data related to an organization/asset/inspection and so on.
- All authorized users should quickly find the most important POIs in an inspection session,
- make their assessment of the data,
- enrich the data with additional comments and analysis, and
- provide feedback and organize actions.
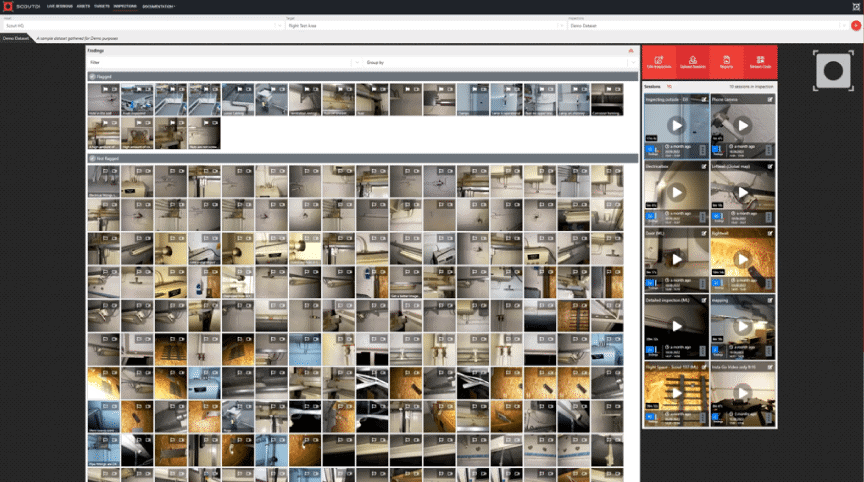
📢Watch this 4-minute video to learn more about the Scout Portal
The Scout137 Drone System can even stream inspection data live to the Scout Portal, a benefit we call live remote inspection. It allows remote stakeholders, like asset owners, class surveyors, structural experts etc.) to take part in real-time, without being present on-site. The data stream from the Scout137 drone contains:
- Live video feed in HD
- 4k photos
- 3D point cloud that can be zoomed, panned and rotated freely
- Location-tagging for every inspection instant
- Establishing a separate voice communication channel via cellphone or a Teams meeting, the combined inspection task force has the power to gather data, assess data and take action on the data while there’s still an inspection crew on-site.
This can be very attractive in some cases. In other cases it is not necessary nor feasible, ref. the bandwidth discussion above.
This is why we keep working with other scenarios, for example a low-bandwidth solution for on-site inspection data uploads: If live remote inspection is not feasible, all inspection data can be uploaded to the Scout Portal as a single .zip file. Even if it takes some time, it allows an off-site stakeholder to replay the inspection in the Scout Portal and assess the data. You can also choose to upload just the hi-res photos.
These scenarios represent a vast difference from:
- having to go offshore and participate in person, or
- waiting for someone to travel back with the memory card.
One of the great strengths of being an end-to-end solution provider is that you get the chance to do this: Design features all the way from drone to portal while keeping focus on who’s gonna use it, what their situation is like and what they need.
An offshore wind example
An example of companies that have taken great strides in their “data-holistic” approach, is evident in the below embedded video: Microsoft CEO and chairman, Satya Nadella kicks off the annual Inspire event with this in-depth look into the Microsoft Intelligent Data Platform.
Also featured in this address is the Microsoft Partner Network video showcasing how Ørsted and Cognite turn offshore wind turbine inspection data into predictive maintenance insights, using the Scout137 Drone for data acquisition and the Scout Portal API for data integration.
Ørsted is a multinational power company and currently the largest offshore wind power developer in the world. Together with Microsoft and Cognite they are set to propel the digitalization of their confined-space inspections forward using advanced inspection-, data- and AI tools.
This example represents a very “complete” inspection data chain, in which inspection data from offshore installations is acquired by drone and turned into actionable information in a larger data ecosystem. It creates a safer situation for the “data hunters” inspecting the wind farm and saves them time, which they can use to harvest more data. Their data is quickly put to use on operational and corporate levels to create insights for predictive maintenance.
The inspection crew is in this case reduced from 4 persons to just 2. Plus a drone. The crew stay safely outside while the Scout 137 Drone collects all the data inside the confined space of the turbine. The location-tagged data is integrated to Cognite Data Fusion via the Scout Portal API and also uses crack- and corrosion detection algorithms embedded in the Scout Portal.
Much of the same benefits can be reaped simply using the Scout Portal’s built-in data management and analysis features, but in this case they went all-in and integrated inspection data with other data. Truly inspiring! 👍
8< – – –
Opinions on this topic? Let us know on LinkedIn 👍
The next step
Are you looking to digitalize your operations and start collecting inspection data from your own assets or on behalf of others? Need a complete, cloud-based data management, analysis, reporting and backup service to with the drone system? Submit the form below to get in touch with us and we’ll help you look at your options!
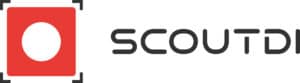