To Simon Ruddick, a combined visual and UT drone platform could mean a welcome goodbye to rope access and scaffolding.
Ever since he started out as a trainee in a local UK company in the late 80s, Simon Ruddick has been inspecting and surveying ships for a living. He is now director at Marine Inspection Services Ltd. and a leading expert in visual surveying and non-destructive testing (NDT) of ships and offshore installations.
The men in the middle
All commercial ships are built to the standards of class societies, laws and international conventions, and they are surveyed repeatedly for compliance. A vessel simply cannot operate without being certified by a class society.
Ultimately, the owner is the one responsible for the safety and integrity of the vessel and the staff. But tremendous responsibility rests on the classification societies, and the limit to their liability is a matter of continuous discussion. To maintain a reliable classification process, it is vital that they remain an independent third party and avoid conflicts of interest. For example, they must be able to demand high-quality inspection data of good coverage as a basis for their assessment, without being responsible for producing the data themselves.
Therefore, the vessel owner must arrange the inspection data to be produced by someone with the necessary expertise, equipment and focus. I.e. the inspection companies.
It’s a job that involves entering enormous, emptied cargo hulls, cargo tanks, ballast tanks and other enclosed spaces to assess their structural integrity. You must know what you’re doing, to gather all information in a safe manner. Got an inspection job that is dark, dirty and dangerous and where tremendous values are at stake? That’s when you call companies like Marine Inspection Services.
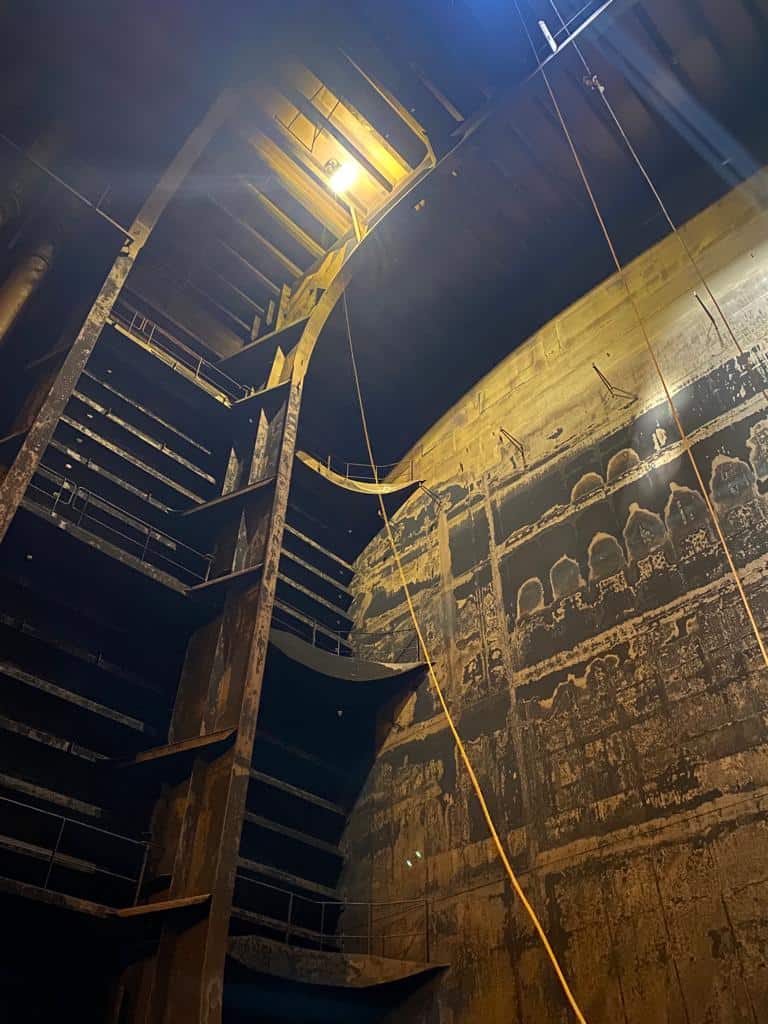
Drone inspections are an important safety measure as they can replace lots of hours of working at height. Drone inspections also save lots of time and money and allow for much more flexible and efficient inspection schemes.
Structural integrity
“On an oil tanker, these tanks are typically about 20 meters high, 20 meters wide and, say, 27 meters long,” says Ruddick. Surveying just a single tank for corrosion or other damage is a comprehensive process, traditionally requiring working at height and a lot of time.
Workers traditionally use ropes and harnesses to climb inside the tanks to access all the surfaces. Sometimes even needing to put in place gigantic constructions of scaffolding. Needless to say—operations like these take up a lot of resources and time.
Through advancements in technology, a lot is changing in the industry. Surveyors are now able to automate processes with real time reporting, doing visual inspections remotely by drone.
“In many cases you’re removing the need for the surveyor to be up on the structure on scaffolding which takes days to put up and costs a huge amount of money,” says Ruddick.
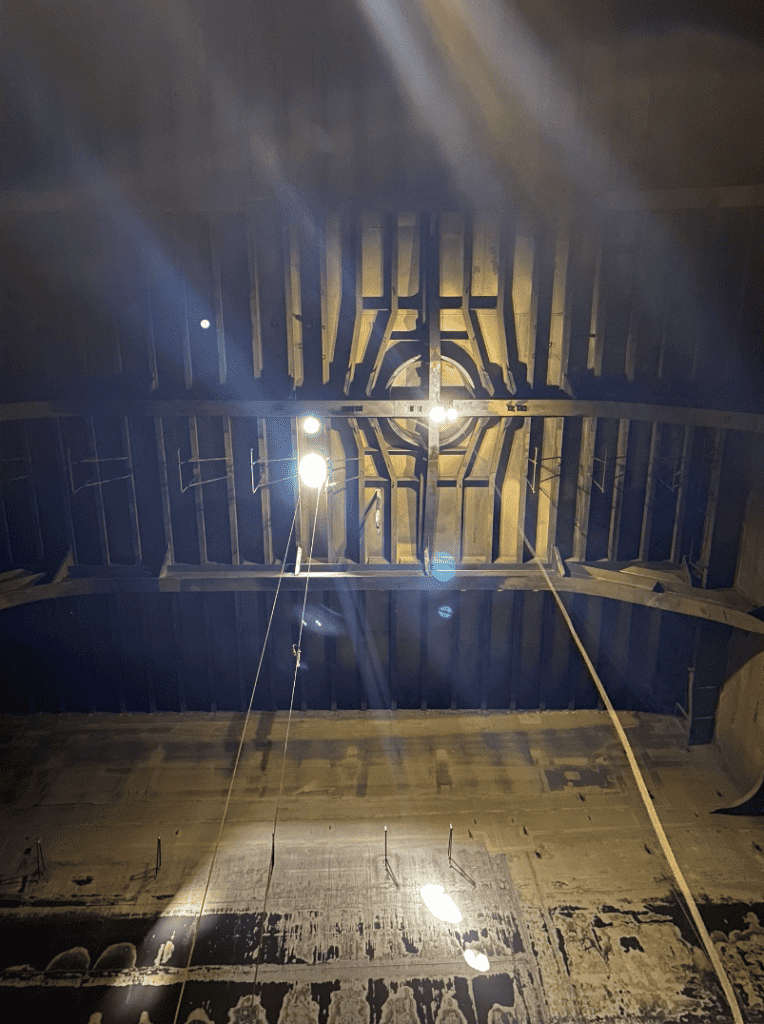
Photo courtesy of Marine Inspection Services.
Non-destructive testing
However, climbing, scaffolding and manual readings are still required for some tasks, such as ultrasonic thickness measurements (UTM). Years of use in rough conditions wears at the metal plates in the construction, the degradation being potentially invisible to the naked eye and to most cameras.
Measuring the plate thickness to gauge exactly how much is corroded and how much is left, is vital to assess structure integrity.
There is also Magnetic Particle Inspection (MPI), which is often used to determine surface cracks, or slight sub-surface defects.
Eddy current techniques are also used to assess welds and to find cracks. Such techniques have the advantage over MPI that it does not require coating removal.
But UTM is the technique for plate thickness and corrosion assessment inside vessels. So in terms of structural integrity assessments, visual and UTM equipment gets you the data you need, when you know how to get it.
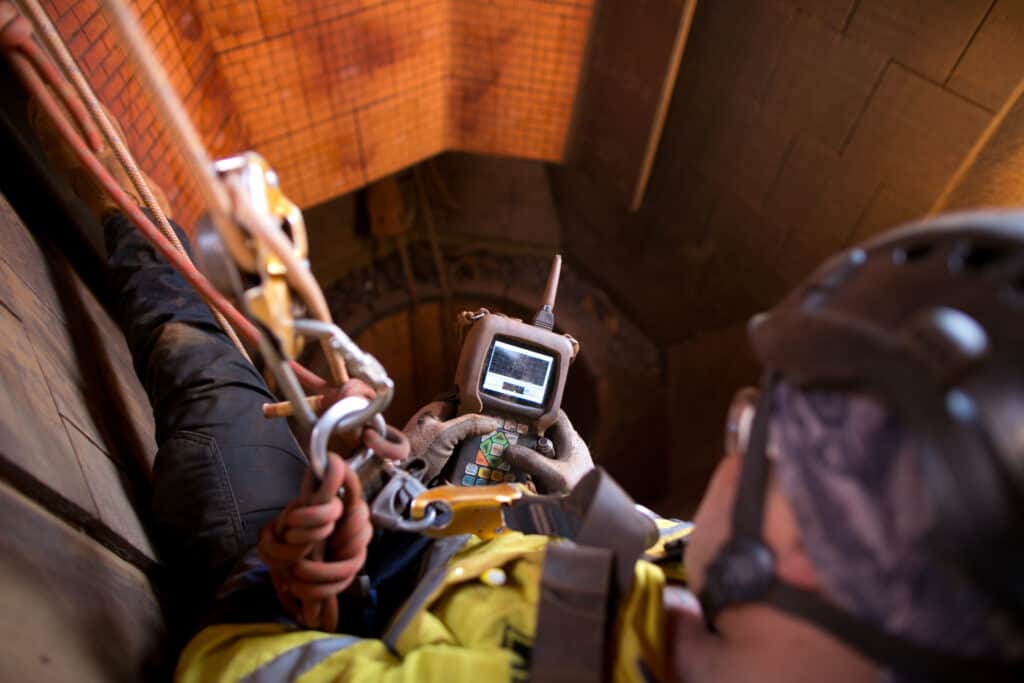
Right first time
The employees of Marine Inspection Services are a small team of sought-after experts that travel the world doing their thing. Sometimes, they will get on a ship in one port, do the survey while it’s sailing and get off at the next port. They normally travel as a team of two or three and may be away for weeks at the time.
Over the last decade or so, using drones has increasingly become a big part of the job.
With the ship’s schedule and cost of cleaning for inspection, it’s critical to work efficiently. You must get it right the first time. “Because you really don’t get a second chance. When you come out of the tank, that tank is closed and you’re not going back in there. It’s so much effort for everyone to get the tank ready for you to come out and say, ‘Oh, I’ll have to go back and get some more footage’.”
“Today we’ll typically be doing a combination of using the existing structure—walking around on the platforms or stringer levels—as well as doing rope access and using drones,” says Ruddick. “The drones go up quickly and give us good results across the different structures, to look at the condition, look for cracks, look at the coating and so on.”
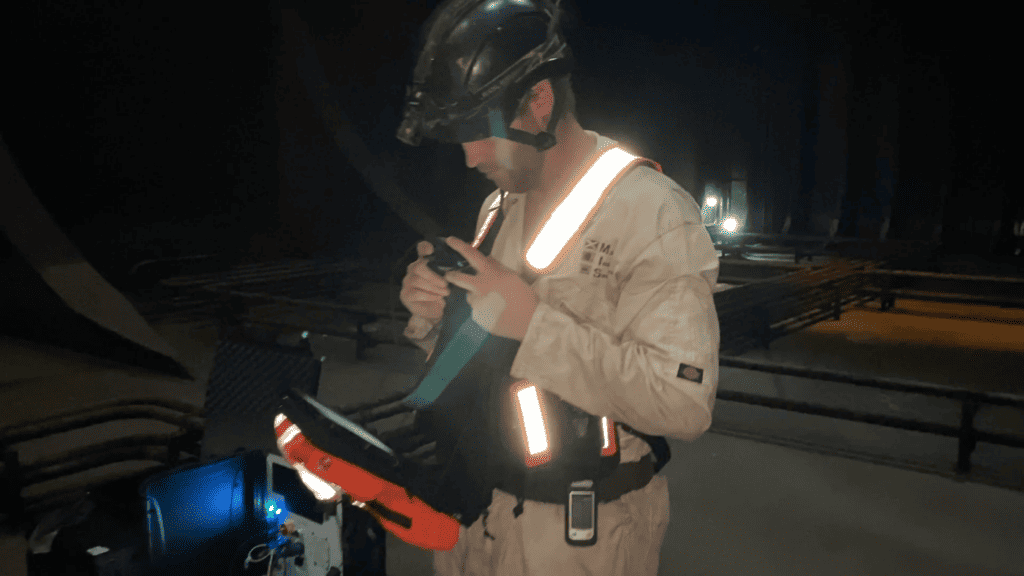
The drone simply brings your eyes to where you need them. Mr. Ruddick refers to the drone as a ladder to get to the structure enabling you to do your job once there. And it records everything, too!
The Scout 137 Drone captures 4K video and photos and uses a 3D LiDAR-sensor to map the entire space in 3D—and the drone’s exact position within that space—in real time. The pilot can fly the drone beyond visual line of sight (BVLOS) and know exactly where it is and where it’s heading all the time.
This is very handy even if you go inside the tank. For example, you may remain on the lowest stringer level and even inspect that from the underside, without climbing down to the floor just for visual line-of-sight to that final part.
“You put the drone in and you do a full visual inspection across the top of the tank, something that otherwise would require scaffolding or rope access. For an oil tanker, this would take days to do without the drone—if not weeks, and thousands and thousands of dollars. With the drone, it’s a matter of hours,” he says.
Tethered drone for stress-free inspection
As opposed to other, battery powered drones, the ScoutDI drone is tethered. That means the operator doesn’t have to worry about losing signal or power or having to fly back and forth changing batteries.
“With a battery-powered drone, remaining battery life is constantly in the back of your mind,” says Simon Ruddick. “If you’re doing a whole tank, then you’re constantly remembering, okay, let’s get this frame done with this battery, and then we’ll come down and then we’ll do the next bulkhead with that battery.”
“Whereas with a tethered drone like the ScoutDI one, you don’t need to think about that. It’s not even in your mind, so you concentrate more on the inspection side of things,” he says.
Using the drone saves a lot of time and effort and allowing this level of focus on the job is an important safety factor. One caveat, though, is that you still sometimes have to go climbing anyway. But this too is about to change.
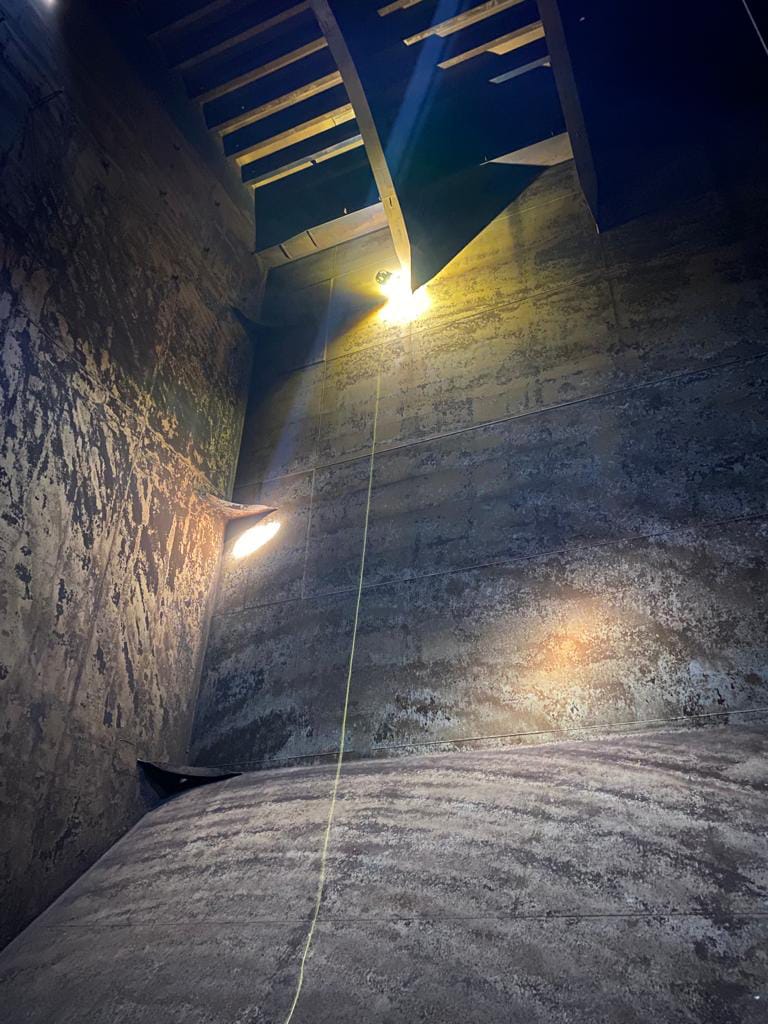
Two birds, one stone
As said, you often have to do both visual inspection and non-destructive testing (NDT) to survey a ship according to class requirements. The latter is done with Ultrasonic Thickness Measurements (UTM). Even if you use a drone for the visual part of the inspection, until now someone—a person—has still needed to go up using ropes or other access methods and bring a handheld measuring probe.
You may save lots of time on visual inspection with a drone. But if you still need to put on that harness and climb around for the UTM part after the drone is back in its case, then there is still room for improvement on the timesaving. Not to mention data coverage.
“If you’re doing manual UTM, then normally you’re only doing sample locations. So for instance, the thickness measurements with rope access might take one day, but that is only sample locations. You’re covering a tiny percentage of the tank and it’s taking you half a day or even multiple days,” says Ruddick.
Manual UTM is vital but time-consuming and only sampled, fractional coverage is practically achievable. Wouldn’t it be nice if a drone could do both the visual inspection and the UTM part? This could enable a small team to complete a job in half a week, that used to take a dozen workers 45 days or more.
[Text has been edited since the UTM Payload has been released since the article was first published]
ScoutDI has enabled visual inspection and UTM in the same drone platform, via the optional UT Measurement Payload that can be mounted on the Scout137 Drone without requiring a separate drone.
As a world first, both the resulting visual and UT data is location-tagged. So when you replay the inspection in the Scout Portal, you can see precisely where any specific piece of footage or UT measurement was taken.
With the possibility to add a UT add-on to the drone, the thickness measurements can be done remotely. Not only saving you time, but the measurements can be done more quickly and thoroughly as well. This is a game-changer for inspection of many types of assets.
“We do lots of chemical tankers as well, and for such cases UT on a drone is brilliant because they are much cleaner than oil tankers. You don’t have to scrape off the thick residue from the crude oil, so you can in fact do the entire job just using the drone.”
If you can eliminate climbing from structural assessment jobs, great benefits in terms of safety, time and cost are unlocked. Offering visual inspection with a camera, and UT measurements in the same drone platform, this is exactly what we’ll be doing.
The drone reaching all the same locations as a climber, and much faster than a climber can, you no longer have to be content with only sample locations. Much greater coverage is within reach and consequently a much more comprehensive and reliable dataset.
A long-awaited change and a major step on the way to digitalization of heavy industries.
Want to know more about visual inspection and UTM using drones?
Are you looking for drone-based inspection technology for confined industrial spaces? Submit the form below to get in touch with us and we’ll help you look at your options 👍
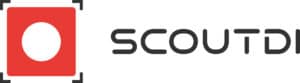