This most anticipated addition to the Scout 137 Drone System enables Ultrasonic Thickness Measurements (UTM) and visual inspection with a high-resolution camera during the same inspection session, without switching payloads or sacrificing LiDAR data.
NEW! Scout 137 UTM payload ready to order
Say hello to the Scout 137 UTM payload. Well integrated with the Scout 137 Drone System, it is a natural extension of our end-to-end confined-space inspection data solution. The Scout 137 UTM payload is now ready to order. Watch the video below for an introduction.
Most requested product roadmap item
The perhaps most requested addition to the Scout 137 Drone System, is also one of the hardest to do well. A flying high-resolution camera is an impressive feat. Especially with unlimited flight-time, LiDAR-based stabilization, location-tagged data and a promising autonomy roadmap.
But designing a flying platform that gets in physical contact with the surroundings is a different story.
Typical scenario
A typical scenario for cargo or storage tank inspection is to collect the visual data first. A drone does a GVI of the asset and then commences CVI sessions in a way that makes sense data-wise or according to how the asset is organized.
Sometimes, additional NDT is required. Most often, a team of rope-access technicians enters the asset and performs thickness measurements with hand-held gauges. The UTM scope and plan is often based on findings from the visual inspection.
Clearly, there is room for improvement in many such projects.
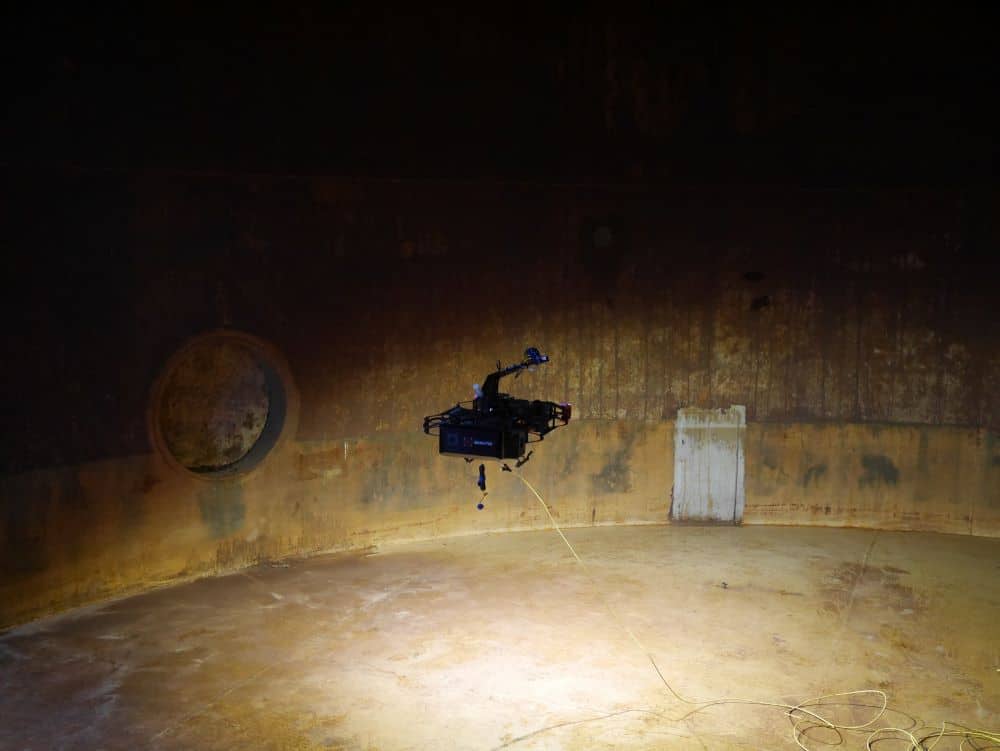
Testing the Scout 137 UTM payload in a steel storage tank
Challenges of confined-space NDT
First, for rope access technicians there is no BVLOS operation. They must enter the asset. For larger assets, entering and evacuation by itself becomes time-consuming and tedious.
In many cases the team can only stay inside for short periods, so either more teams must be available, or coverage and completion time suffer.
A confined space inspection drone requires a team of typically 2 people to work inside the asset for a much shorter time, often requiring just a single shift for completion. Not forgetting the most important safety benefit: No team member has to be working at heights.
If the drone is also BVLOS-capable, the team can stay on the upper deck, controlling and monitoring everything remotely in open air.
Many of the above concerns are relieved with the upcoming addition of an optional UTM payload to the Scout 137 Drone System.
Contact operations with indoor inspection drones
For any inspection drone, there is a constant weight budget battle. Adding payloads adds weight.
For UTM, the payload includes coupling gel. There will be a hard limit to how much the drone can carry, and for battery-powered platforms this eats available flight time.
You must be able to keep the drone steady when approaching the surface, even in tight spots where turbulence and protruding features may become threats.
The mechanism designed to maintain adequate contact pressure, must be easily reversible: After reliable measurements are acquired, the drone must be able to disengage from the surface in a controlled fashion and move back out to a better flying space or on to the next spot.

Thinking inside of the box
Using throttle to maintain surface contact is one possible path and might be the first that many would think of. It has the most potential in drones with flexible thrust vectors paired with a precise control loop. Without these two factors, it would be very hard to keep the platform from moving in contact with the measured surface. Especially with slanting surfaces.
This type of solution would require a complete redesign of the Scout 137 drone platform and is therefore not interesting in the context of offering an “optional payload” on an existing drone. We must stay inside of the physical and mechanical constraints of the current platform, while allowing integration of external sensors and actuators.
Magnets are interesting because they make the steel plates hold on to the UTM probe! If the surface is smooth enough, the probe head stays in the same spot throughout the measurement while a good and flexible mount allows the drone to move without wiggling the head out of position.
In order to enable UTM on surfaces of different angles (wall, ceiling, slanting beams or plates), the probe head is fitted with a servo, so that the angle can be adjusted ± 90 degrees.
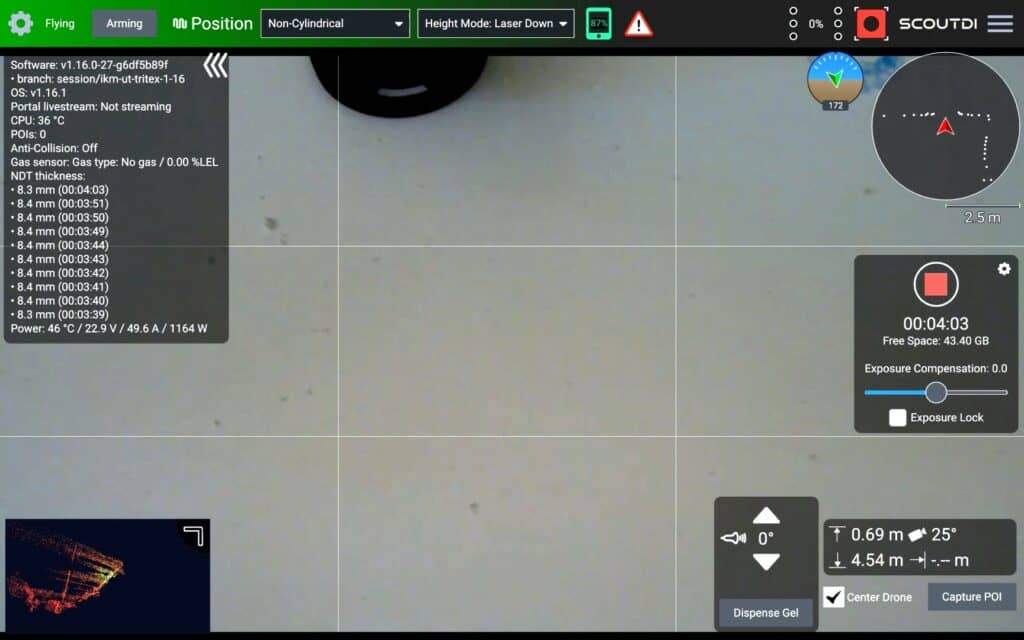
This is how a UT measurement looks via the Scout App: The camera is here tilted 55°, nicely catching the UTM probe. A laser mounted on the probe provides further guidance. Data readings come in automatically (grey window to the left) when contact is detected. The pilot disengages the probe from the surface by clicking a controller button.
The innovative design of the adjustable and flexible probe head mount (patent pending) also allows a smooth release of the drone from the measured surface: An automated probe head movement releases the magnet and allows the drone to move away from the surface.
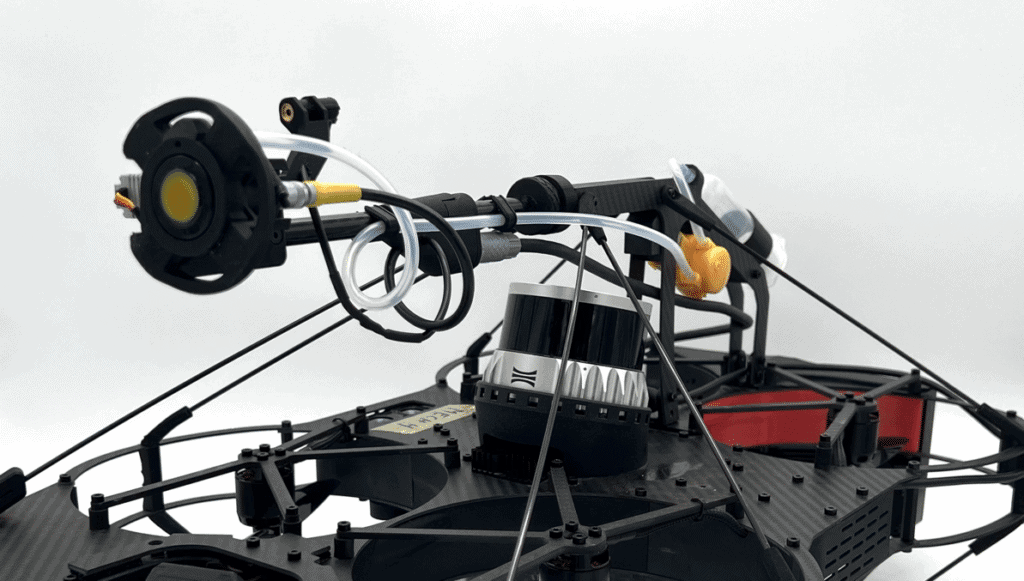
Scout 137 Drone System with UTM payload (the flexible probe head mount is pat.pend.).
UTM starts automatically when the probe detects contact with the surface. Release is initiated by the pilot to allow groups of measurements for as long as necessary. The pilot can watch the readings appear in the Scout App and decide when to initiate probe release.
Watch the video below for an introductory overview to the ScoutDI UTM solution in practical use 👍
Scout 137 UTM payload: What you’ll be getting
With the upcoming Scout 137 UTM payload, several of the previously mentioned concerns are already solved:
The Scout 137 drone system has been designed for no human entry from the ground up. The onboard 3D LiDAR handles positioning and mapping and provides visual and spatial awareness support to the pilot together with the 4K camera. If inspecting a large cargo tank, you can see where you are and where you’re going without leaving the stringer level you’r e on, possibly without entering the tank at all.
The LiDAR also location-tags all data captured by sensors integrated to the Scout 137 data flow, so far including camera and UTM data. When uploading all session data to the Scout Portal, locations of visual and UTM data are clearly marked and color-coded in the 3D point cloud.
Combining presentation of two datasets like video and UTM this way, gives advantages beyond just looking at both datasets on the same screen:
- You can see where the photo, video or UTM was captured, so you know immediately where action is needed
- You can relate the UTM to visual data to consider probable causes
- Vice versa, visual attributes may give clues of important UTM to prioritize
- You can easily make a general assessment of the data sampling coverage, since the distribution of all measurements is shown on the point cloud.
- Video adds further context to everything
Of course, all data is securely stored and backed up in the Scout Portal.
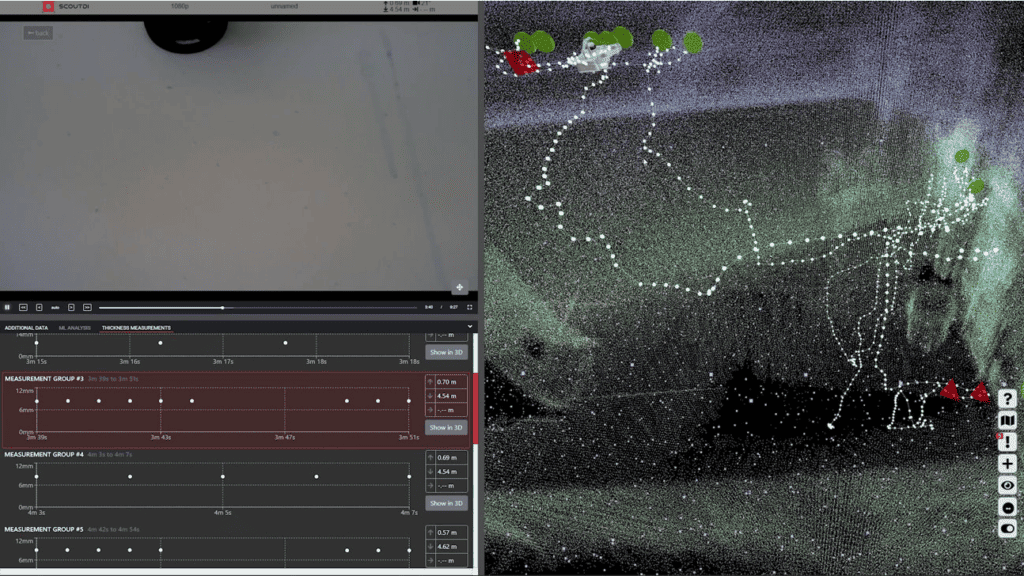
Snapshot of the above flight session from the Scout Portal: Visual POI and UTM are marked and color-coded along the flight path. Clicking a UTM data point opens that measurement group and moves the play head to the correct position in the video.
The Scout 137 UTM payload is an optional payload, well integrated with our existing solution for visual data. It consists of the probe, mount and arm, coupling gel reservoir and pump, all the necessary cables and a small PCB that is mounted inside the drone body.
The Scout137 UTM payload is designed to improve situations as described above. On the operations side, when UTM is done following visual inspection, it will in many cases allow the inspection crew to avoid working at heights and may eliminate human entry altogether.
In other cases, the drone solution will be a welcome complement to rope access. Especially suited for repeated measurements across large surfaces, rope access technicians may reduce their work scope significantly by allowing the drone to focus on the areas where it can move freely and quickly.
The intention is to present an efficient and robust add-on to maintain safety, accelerate project completion and improve data coverage.
What you’re not getting
Reliable UTM requires good contact with the surface of the plates being inspected. In many cases, this means that the surface must be cleaned of any product residue, corrosion and other artifacts that affect the smoothness and texture of the surface negatively. It also means that debris must be removed from the probe magnets from time to time.
Hence, getting a drone to do the UTM will not necessarily take away the need for cleaning, scraping or grinding that was there in the first place, but it will be an excellent tool for screening of condition and reduce the scope for rope access or scaffold-accessed NDT inspection.
Summary
A UTM option for the Scout 137 Drone System is being developed and subjected to extended industrial testing. It is intended as an efficient add-on to maintain safety, accelerate project completion and improve data coverage of visual and steel plate thickness data of large assets.
When ready, the UTM option can be ordered with any new drone purchase from ScoutDI. In some cases, it will also be possible to retrofit it to already purchased systems. For more information, please email sales@scoutdi.com or submit a contact request for on https://www.scoutdi.com.
Tell me more about the Scout 137 Drone System!
Contact us using the form below👍
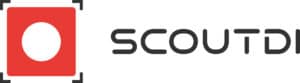