Revolutionary FPSO inspection with No Human Entry and Class Sign-Off: Read about the Shell “Turritella” Special Survey, where the Scout 137 and the UTM Payload played integral roles.
We at ScoutDI are excited to share our involvement in a groundbreaking project that has set a new standard in offshore inspections. The project achieved class sign-off by the American Bureau of Shipping (ABS) and represents the world’s first fully robotic COT (Cargo Oil Tank) Special Survey with No Human Entry.
Conducted on the FPSO Turritella, operated by Shell, the Survey was completed with no diving, no work at height and no human entry into confined spaces, while the vessel was at sea in the Gulf of Mexico. This achievement marks a significant milestone for the FPSO industry and the broader field of industrial inspections.
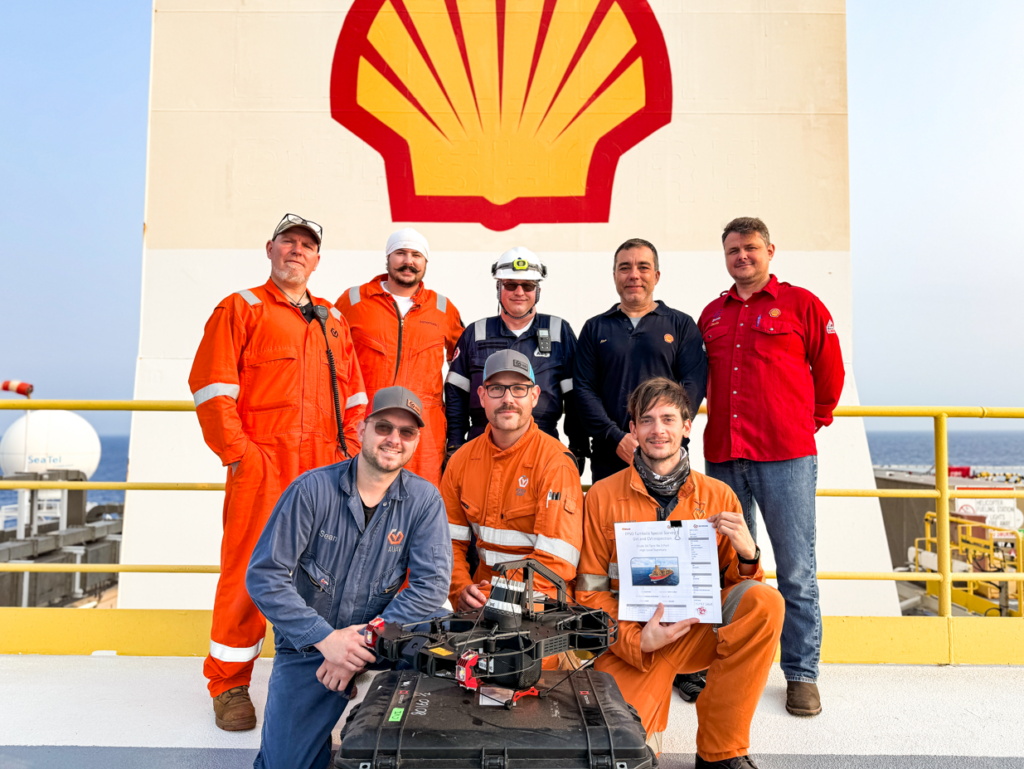
Captain Aleksandar Zhechkov, Marine Supervisor Claudiu Iordache and the inspection team posing with the Scout 137 onboard FPSO “Turritella”.
iCOT: Pioneering Remote Inspections
This project is the culmination of years of innovation and collaboration between Shell and CWL Group companies Geo Oceans, Sonomatic, and AUAV, who have worked together to develop a groundbreaking approach to performing unmanned water ballast tank, cargo oil tank, and hull inspections without the need for confined-space entry or diving activities.
Named iCOT, the approach involves the use of several robotic tools to perform comprehensive internal inspections entirely remotely. The Scout 137 Drone System and the UTM Payload are integrated into iCOT as vital data acquisition tools for the inside of Cargo Oil Tanks (COT).
This important technological achievement was awarded the 2024 Craig Black Innovation & Technology Award.
Photos from the Turritella COT inspection.
Value drivers for Shell
To Shell, the operator of FPSO Turritella, the primary value drivers of the robotic initiatives are clear.
iCOT technology enables the complete inspection of cargo oil tanks and similar confined spaces without the need for human entry. This is particularly important for enhancing safety and efficiency in offshore operations.
In the data dimension though, lies the key to transforming the industry long-term.
Robotic inspections result in data sets from multiple sensor types; cameras, thermal cameras, LiDAR sensors, UTM probes, gas detectors etc. Structured and standardized, these data sets can be integrated to provide new insight and allow filtering and searching.
This wealth of information is crucial for supporting integrity management decisions and represents a significant advancement in the safety and efficiency of FPSO operations. Soon, the door opens to Machine Learning, Computer Vision and Autonomy.
Down the line; as we continue to scale these solutions, there are no more humans working at heights or in confined spaces. And perhaps not that many travelling experts with limited availability either. The robots are online and enable real-time global collaboration, 24/7.
COT inspection with the Scout 137 Drone
The Scout 137 Drone System was used for cargo oil tank (COT) inspection during this special survey. This part of the survey was carried out by drone service specialists AUAV, part of the CWL group and sister company to Sonomatic and Geo Oceans.
The Scout 137 Drone is tethered and has unlimited flight time. It is therefore uniquely suited for inspections in such large, complex environments like FPSO cargo tanks.
In this project alone, between 35 and 40 drone flights were conducted, acquiring over 40 hours of data. Having the battery-free, fully wired solution allows full focus on the navigation and data collection aspects of the job.
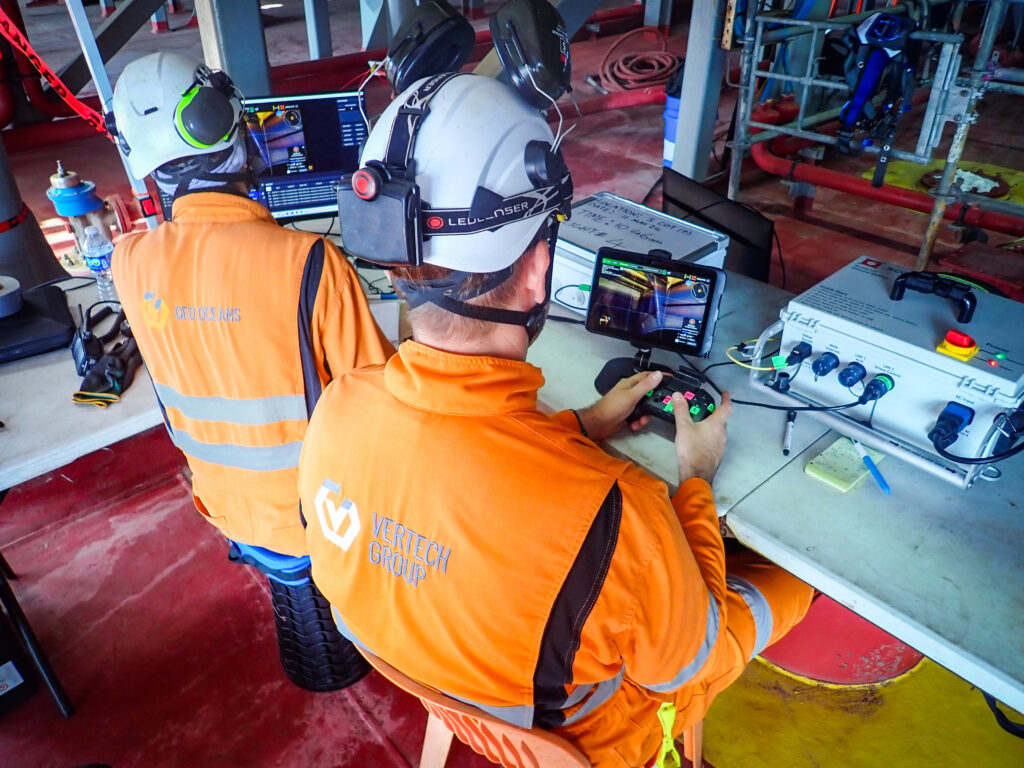
The inspection crew monitoring and controlling the inspection from top deck.
As previously stated, no humans entered the COT during this inspection: The entire operation was done BVLOS (Beyond Visual Line of Sight). Using dual screen setups, all the involved could follow the job from the top deck. Surveyors and drone operators could discuss and make decisions as the operation proceeded.
The onboard 3D LiDAR provides the foundation of the BVLOS aspect. Paired with advanced processing algorithms, it ensures rock-steady positioning and provides drone crew with the confidence to bring the camera close when needed, or even get into surface contact as required for UT Measurements. It also provides the location information needed to pinpoint where any data point was acquired.
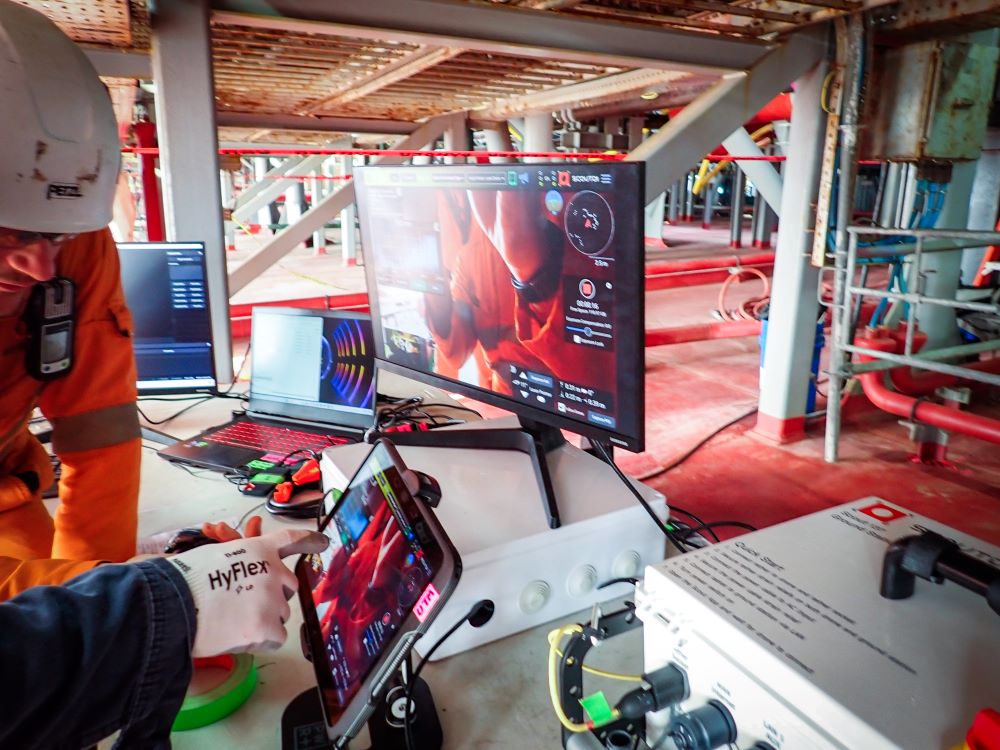
No need to look over the pilot’s shoulder. The Scout App screen is easily shared to multiple screens so everyone can see the video feed live and understand the drone’s situation down in the tank. On-screen A-scan allows real-time evaluation of UT measurements and the tether allows all the time in the world to agree on the proceedings and get the survey done right.
This way, the spatial awareness provided by the 3D LiDAR is valuable during flight and continues to make a big difference after the drone has landed, i.e. in the Scout Portal.
The Scout Portal
The FPSO “Turritella” is connected to the internet via a broadband fiber connection. Although not currently the standard in offshore environments, it provided a useful advantage to the Shell onshore civil marine structural integrity team.
“By using the Scout Portal, our civil marine structural integrity team could assess fresh data every day to ensure the inspection team onboard captured the needed data at the right quality.”
– Steven Trevino, Deepwater Robotics Program Manager at Shell
As the Geo Oceans team uploaded inspection data every day, Shell’s structural integrity team onshore were able to follow the inspection closely and verify all data while it was still fresh. An unprecedented capability to stay connected to the inspection crew.
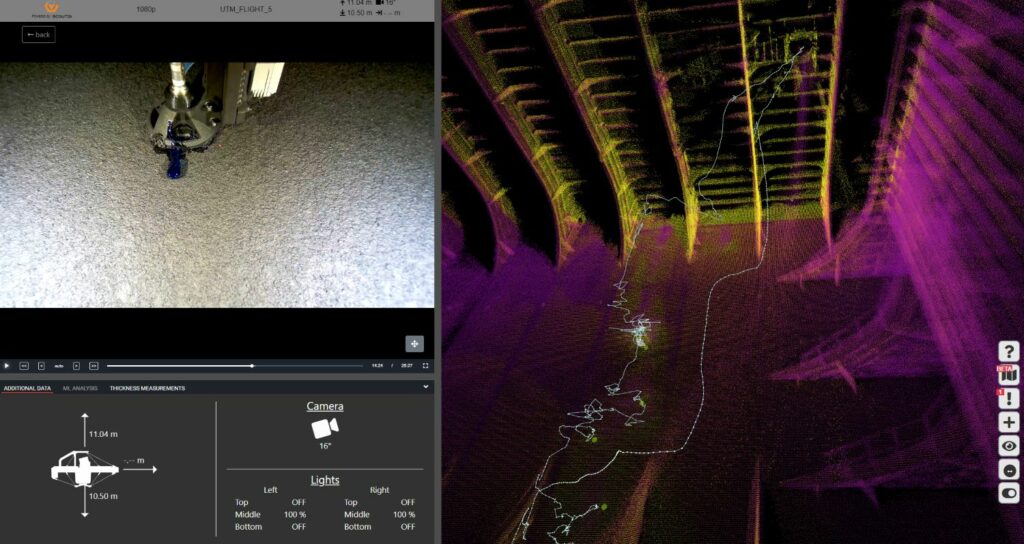
Screenshot from the Scout Portal: UT measurement at about mid-height in a Cargo Oil Tank. UT Measurements are marked with green, clicking brings up measured values and A-Scan curves.
Implications for the Industry
The implications of this project extend far beyond the immediate scope of FPSO operations. Traditionally, cargo oil tank inspections have required human entry into confined spaces, an activity with inherent risks. Previous attempts at robotic inspections have always required some level of human entry to meet survey requirements.
However, this project marks the first time that an entire inspection process was conducted 100% remotely, meeting the stringent standards of ABS without the need for any manned entry. Capitalizing on this success, a total of 4 tanks were accredited during the first deployment offshore.
The principles demonstrated here—comprehensive data collection, high-precision inspections, and remote operations—are widely applicable and have the potential to revolutionize industrial inspections across the board.
Looking Forward
We are excited about the future possibilities for remote inspection technologies. The successful completion of the world’s first fully robotic and BVLOS FPSO Cargo Oil Tank Special Survey, with class sign-off, is a testament to what can be achieved through innovation, collaboration, and a relentless pursuit of excellence.
It has now been shown that with the right tools and collaborative effort, it is possible to achieve safer, more efficient operations in some of the most challenging environments. ScoutDI is looking forward to contributing to the ongoing evolution of inspection technology 👍
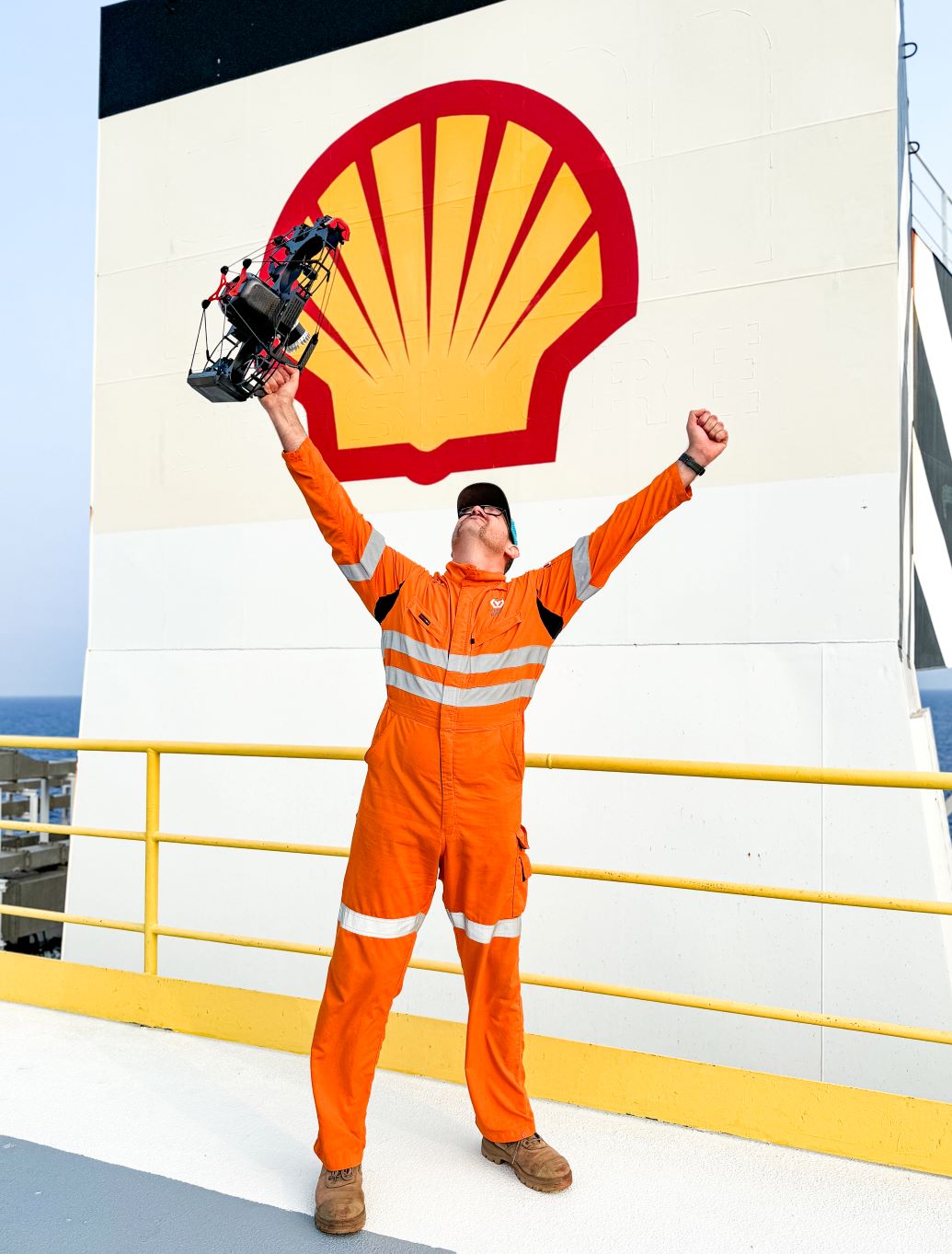
100% Robotic inspection, no humans entering confined spaces or working at height.
Job well done!
Would you like to know more about the Scout 137 Drone System?
Feel free to contact us using the form below! 👍
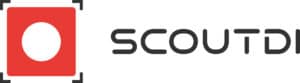