Case Study
Non-entry inspection of pressure vessel
The backdrop of this demo inspection is the appointment of ScoutDI as one of the winning robot technology providers in SAFETYTECH Accelerator and LRQA’s initiative. This is an important and commendable move to drive industry uptake of new technology that ScoutDI is very happy to participate in. The comprehensive trial programme has now started, and this pressure vessel represented the first trial.
Allnex is the leading company globally for industrial coating resins, crosslinkers and additives. Having a pressure vessel scheduled for internal inspection, they generously hosted the trial on their premises in Bergen-op-Zoom, almost one hour south of Rotterdam.
Time Savings
Reduced asset down-time through flexible inspection regimes
Cost savings
Reduced cost by avoiding scaffolding, climbers and rescue teams
Safety
Improved safety by reducing need to enter hazardous areas
Quality
Improved data quality and situational awareness in data capture
Preparations
Arriving on site, we met with the reps from Allnex and LRQA. After a security briefing and some dressing up, all we needed was an extension power cord before meeting with the inspection target: We would be inspecting a pressure vessel for Nitrogen storage. A horizontal cylinder measuring 10m in length and 3m in diameter, all yellow and shiny. While empty at the time of the inspection, the geometry and dimensions represented some interesting challenges.
An interesting aspect was that no persons were allowed to physically enter the pressure vessel. The setup for the inspection therefore became this:
- Two men with radios and a drone system. The pilot, or operator, remained on the ground.
- The inspection assistant climbed the scaffolding to the topside of the pressure vessel, bringing the drone.
- Operator and assistant talked via personal radios which allowed communication without taking eyes or hands away from what they were doing.
We also prepared a new inspection project in the Scout Portal, in order to stream the inspection live to off-site stakeholders. Read more about this below.
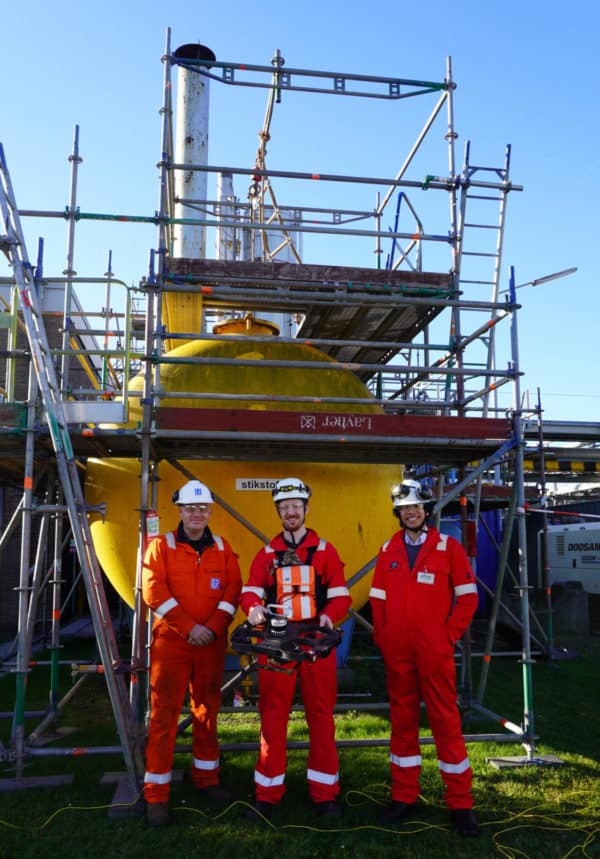
All dressed up and ready to go
LiDAR drone
The advantage of using LiDAR for inspection within confined spaces becomes even more obvious when you need to inspect an object that you cannot enter. The Scout 137 is equipped with a 32-beam scanning LiDAR and uses its output data for mapping, localization, obstacle detection and as visual guidance to the drone operator.
The operator tablet displays a 3D point cloud along with the live camera feed. This 3D point cloud provides a map of the inspection target with the drone localized at the centre. The operator can rotate, pan and zoom this map to get an overview of the interior and see the drone’s position and orientation inside the pressure vessel. With this, the operator gets an informed overview of the situation inside and can make decisions about where to go and how to get there.
Without it, the operator would fly on camera feed alone, not knowing what’s behind the drone or next to it, nor the distance to the nearest obstacle. It would be especially confusing to navigate inside a symmetrical object with homogenous surfaces, where everything would look like everything else. Like an all bright yellow, cylindrical Nitrogen pressure vessel.
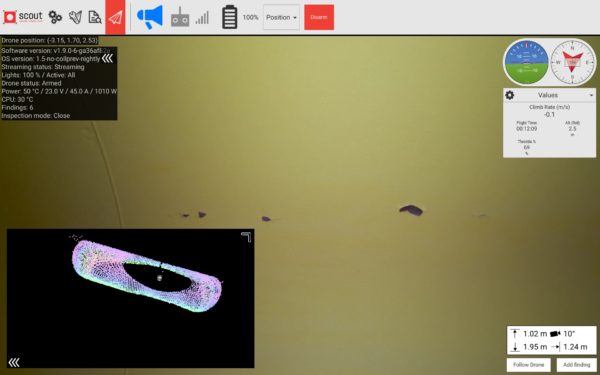
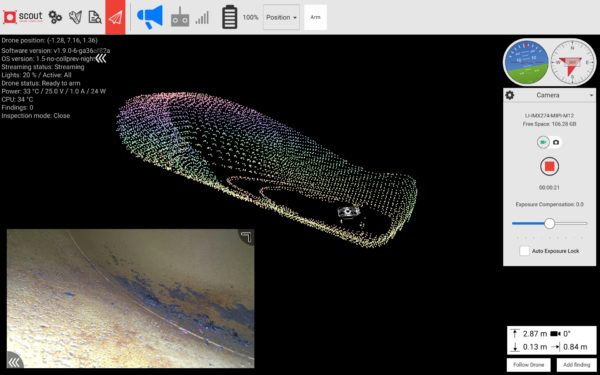
Off-site stakeholders had been given access to the Scout Portal and sent a URL to the inspection. Meeting attendants would simply click the link to open a browser window to the Scout Portal, where they could follow the inspection remotely. Once in the Scout Portal, they would be able to see the live video feed and interact with the LiDAR 3D point cloud; the same information that is displayed on the operator’s tablet.
In addition, an MS Teams meeting was organized so we could make introductions, explain the inspection system and answer questions from the off-site audience while they were watching. This live remote participation generated lots of interest and became an engaged session where the audience kept us busy, asking questions throughout.
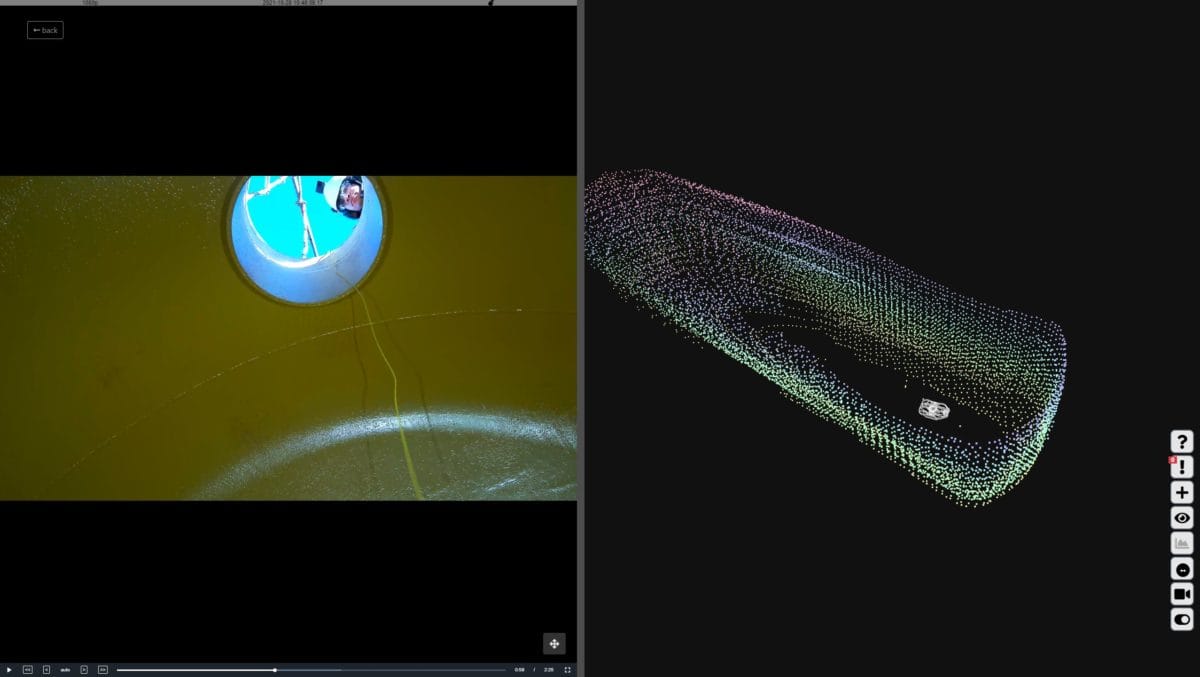
The Scout Portal enables you to participate remotely and see inspection replays anytime and from anywhere.
Catch and release
To launch the drone through the pressure vessel’s very narrow opening, which was smaller than the drone’s length, we had to release it by hand into the pressure vessel. Procedure:
- Assistant extends arm holding drone into the pressure vessel.
- Assistant asks operator to start the drone propellers.
- Operator starts propellers
- Assistant confirms that motors are spinning, and
- Operator increases throttle.
- Assistant confirms that drone has lift, releases drone and confirms to operator.
The drone is then airborne inside the pressure vessel.
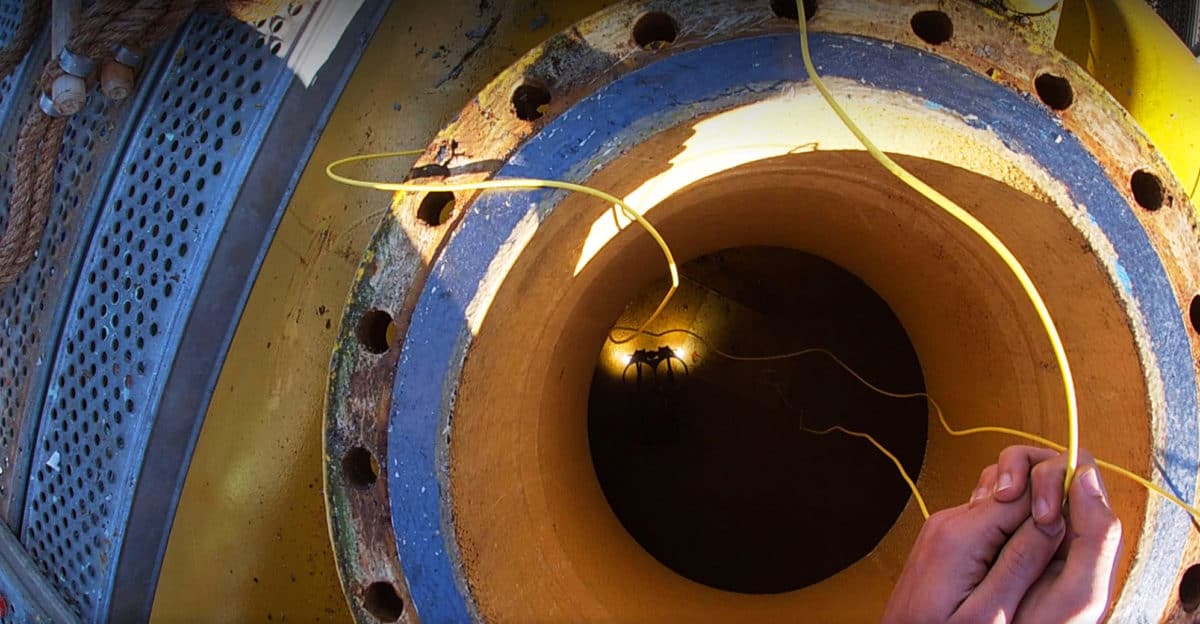
Conclusion
Our Allnex visit turned out to be a very useful and positive experience, to ScoutDI and the other parties involved. It is very rewarding to be able to demonstrate non-entry inspection in such a well-documented trial, while also streaming the whole thing live.
We had some exciting moments tackling the aerodynamics of this narrow, cylindrical pressure vessel: Air currents from the powerful propellers would circulate round the pressure vessel and create turbulence. This is a challenge related specifically to the circular cross-section, aggravated by the small diameter. Flying too close to the walls increases the risk of drone instability.
Our gracious hosts stayed next to the drone operator throughout the job. Giving instructions and discussing details while watching the tablet. This inspection mode was notably improved by the fact that the 3D point cloud was available on the operator’s tablet.
ScoutDI would like to thank SAFETYTECH Accelerator and LRQA for facilitating this trial. We also thank Allnex for providing an asset for inspection and for welcoming us on their premises. And of course, thanks to all the curious audience, on-site and off-site, who contributed to make this a worthwhile and exciting experience for everyone. Tot de volgende keer!
Would you like to know more about the Scout 137 Drone System?
Are you looking for drone-based inspection technology for confined industrial spaces? Submit the form below to get in touch with us and we'll help you look at your options 👍
Learn More
Scout 137 Drone →
The Scout 137 Drone System has been specifically designed to give you control, coverage, and situational awareness for your confined space inspection activities.
Scout Portal →
The Scout Portal is our powerful cloud-based tool for inspection data management, review, analysis and reporting.