Case Study
Steinkjer Water Treatment Plant
Introduction
Water treatment plants are found all over the world. Most plants comprise large indoor facilities and require regular inspections to check structures for corrosion and cracks. Tall structures typically require the use of scaffolding or a team of climbers. This is both expensive, time and labor intensive and it exposes inspectors to health and safety risks.
The Løsberga Wastewater Treatment plant is built inside of a mountain hall in Steinkjer, in Central Norway. The plant cleans wastewater from central Steinkjer and surrounding areas before it is released into the fjord. The capacity is about 24500 person equivalents.
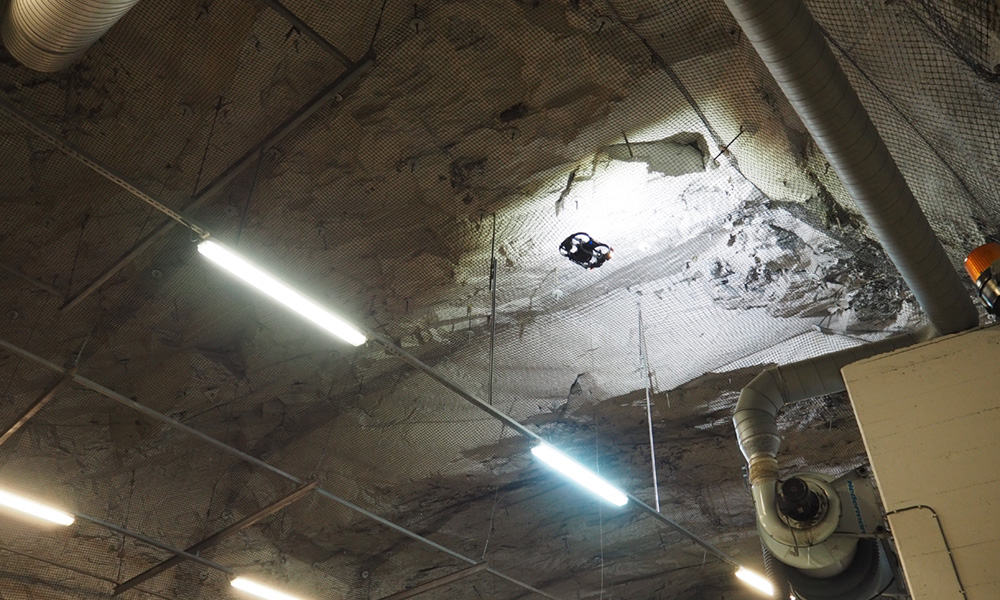
Time Savings
Reduced asset down-time through flexible inspection regimes
Cost savings
Reduced cost by avoiding scaffolding, climbers and rescue teams
Safety
Improved safety by reducing need to enter hazardous areas
Quality
Improved data quality and situational awareness in data capture
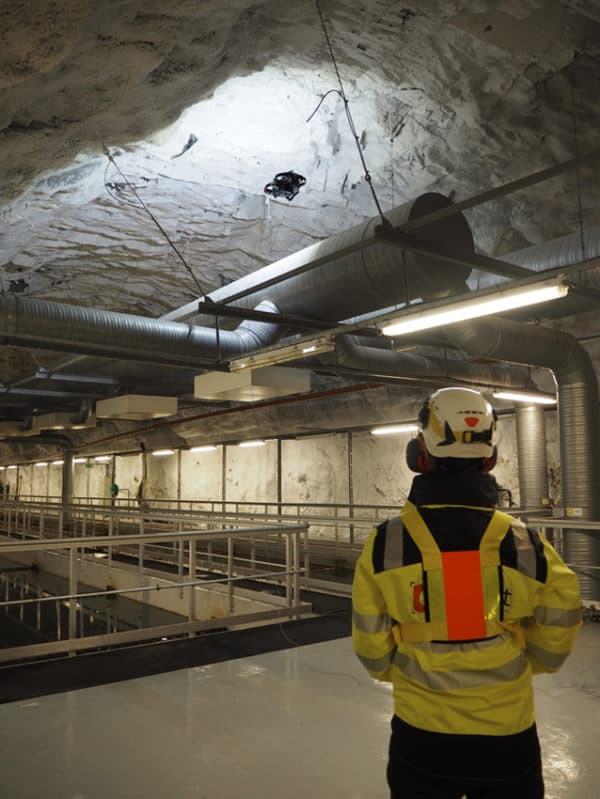
Customer requirements
Due to the presence of corrosive gases, the structures and assets inside the treatment plant are especially exposed to corrosion, cracks, and rapid structural degradation. It is therefore important to perform frequent and regular inspection of the assets. Areas of particular concern are e.g. bolts attached to the ceiling as well as the bolts and wires that secure the ventilation system.
Normally, photos are taken with a handheld camera to record findings or areas of interest within the facility. One of the problems of such photos of specific details is that it is difficult to know exactly at which location in the treatment plant they were captured. It becomes even more difficult to effectively communicate this inspection information onwards to other interested persons.
Results
One key advantage of the Scout drone inspection system is that the inspection data is location-tagged. Algorithms for simultaneous localization and mapping based on the data from the 3D LiDAR is used to create a map in the form of a point cloud of the asset. In addition, the position and attitude of the drone is estimated at every point in time.
In addition, we implemented a more sophisticated collision prevention algorithm that we call “slide-along-wall”. This algorithm prevents the pilot from colliding into obstacles such as walls. Furthermore, if the velocity of the drone has a component in a direction parallel to the collision surface, the drone will start moving along the collision surface at a specified distance.
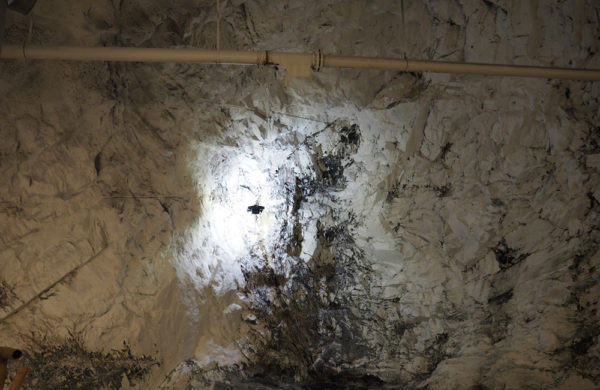
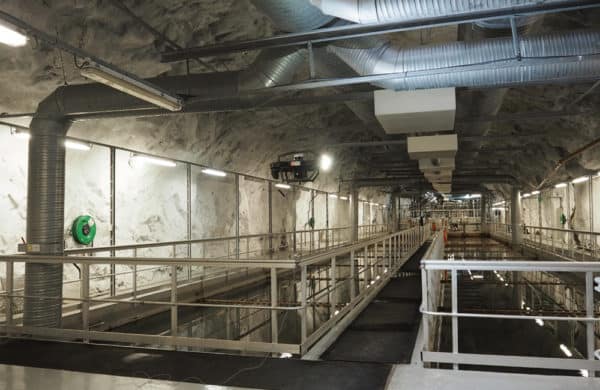
Conclusion
The drone performed well under these conditions, and we were able to verify that the enhanced collision prevention and slide-along-wall functionality was working as desired. Even when we flew above the water, the LiDAR pointing downwards appeared to work and it helped prevent the drone from colliding with the water.
Would you like to know more about the Scout 137 Drone System?
Are you looking for drone-based inspection technology for confined industrial spaces? Submit the form below to get in touch with us and we'll help you look at your options 👍
Learn More
Scout 137 Drone →
The Scout 137 Drone System has been specifically designed to give you control, coverage, and situational awareness for your confined space inspection activities.
Scout Portal →
The Scout Portal is our powerful cloud-based tool for inspection data management, review, analysis and reporting.