Case Study
YINSON adopting new technology for offshore tank inspection
Executive Summary
Yinson Production has performed visual inspection of an FPSO unit in cold lay-up, under the supervision of a DNV class surveyor and via assistance of global inspection company Zener Maritime Solutions. The purpose was to determine the overall condition of the vessel before possible redeployment.
A Scout 137 Drone System from ScoutDI was used inspecting the cargo tanks and an ROV (Remotely Operated Vehicle) operated by AOS Offshore was used for WBT (Water Ballast Tank) inspection. Additionally, an outdoor drone and a hull crawler were used for outside hull inspection.
The drone inspection brought quantified benefits in terms of increased safety, time- and cost savings. As shown below, visual inspection took 1.2 days per tank using the Scout 137 Drone System and would normally take 8 days with a team of rope access technicians.
Continue reading for further discussion of benefits.
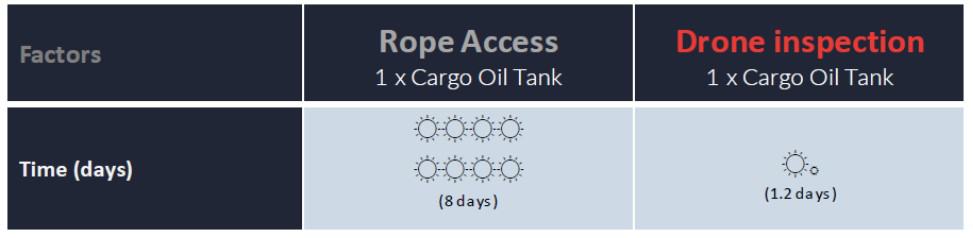
Overview of time usage for inspection of FPSO cargo tank. Additional comments on data coverage and data availability in the discussion below.
Easy access to inspection data
The use of the Scout 137 Drone System and the resulting safety and efficiency benefits are the focus of this article. But it is important to note that the Scout Portal was used to store, present and manage visual data from all the mentioned data-collecting robots. This provides all stakeholders with one well-organized, online digital interface to access all inspection data from the entire project.
Another observed benefit is that work pack compliance can be established in post. Even though a class surveyor was physically present, it was concluded that this is not strictly necessary. Inspection compliance and data assessment can be done entirely off-site via full inspection replay in the Scout Portal.
This saves travel and logistics and offers great flexibility to all the involved. Performing drone inspections as needed during class inspection cycles has clear advantages with regards to operational agility and efficiency, in addition to advantages with safety, cost, data coverage, -quality and -availability.
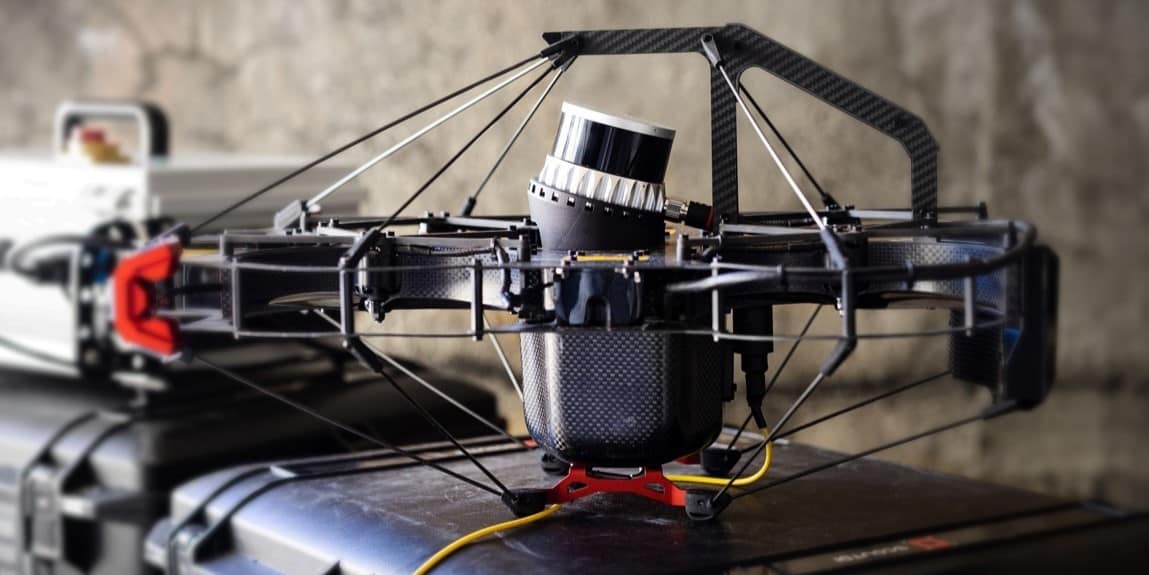
The drone in this photograph is the “next-gen” Scout 137, which is the updated version of the Scout 137 Drone System used in the inspection.
Introduction
Yinson Production is one of the largest independent FPSO leasing companies globally. They are subjected to periodical class surveys to establish structural integrity and general seaworthiness of their fleet. Yinson Production is also a ScoutDI client, owning several Scout 137 drone Systems.
AOS Offshore is a specialist offshore supply company operating a large, growing fleet of subsea, aerial and crawler drones for a multitude of offshore and critical infrastructure inspection purposes. They are also the official ScoutDI sales partner in Singapore.
Zener Maritime Solutions is a global maritime & shipping solutions company headquartered in Singapore, also offering inspection services. Being a global leader in thickness measurements and visual inspections, they offer drone inspection in addition to traditional methods like rope access. They are also a ScoutDI client.
The inspection target in question was an FPSO unit “parked” at a buoy off the coast of Malaysia. It was not in production at the time of the inspection and the purpose of the inspection was to determine overall condition before possible redeployment.
In total 8 cargo oil tanks, 9 water ballast tanks, 1 slop tank and 1 peak tank were inspected, looking for structural anomalies: Cracks or rust, with a particular focus on welding seams. Cargo tanks were emptied, and ballast tanks were full of water.
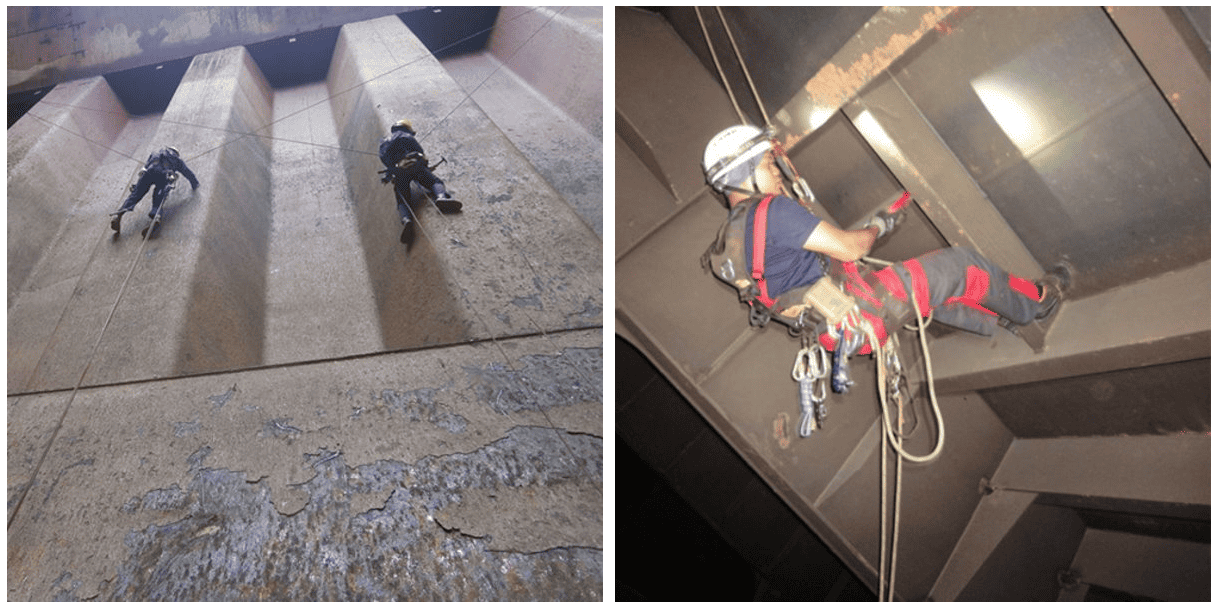
Rope access inspection is a time-consuming method but requires relatively little preparation work compared to other traditional inspection methods. Working at heights this way comes with some risks and requires well-trained personnel working long days.
Preparations and entry
Preparing an FPSO cargo tank for drone inspection takes approximately the same amount of time as for rope access. Rope access is considered an inspection method requiring relatively little preparation, especially in comparison with other traditional methods that require scaffolding etc.
Because it’s non-EX, preparation of tank requires the same set of procedures and time as human entry. These are factors that are not easily mitigated, but also not related to the inspection method.
The reason drone inspection is a huge time saver, is that the actual inspection phase is far more efficient.
Scout 137 Drone traversing under deck area. A drone can quickly reach high altitudes and cover large surfaces very efficiently. Although the preparation time for drone inspections is comparable to other methods, there are great benefits in terms of safety and efficiency, data coverage and -availability.
For cargo tank inspections with the Scout 137, the pilot settled on stringer level 1 with all the gear. This is the highest stringer level, directly under the deck. The class surveyor remained topside in the open air, monitoring the inspection via a screen mirroring the pilot’s tablet.
Even though the pilot was inside the COT, the inspection is considered BVLOS by the definition from the International Civil Aviation Organization (ICAO): “An operation is considered BVLOS when the remote pilot does not use visual reference to the remotely piloted aircraft in the conduct of flight“.
Since line-of-sight was established intermittently on and off during the inspection, it is fair to not consider it a conventional BVLOS operation. Still, in a 25-meter-high tank with 4 stringer levels, a live drone video feed and on-screen LiDAR data support via a 3D point cloud is a substantial advantage to pilot and surveyor.
Working from high-level stringers has safety advantages since personnel is kept away from possible residual fumes and have short routes to nearby entry- and exit points. Another safety benefit is added by not taking off from the floor, since no dust will be thrown up by the propeller blast to cause problems.
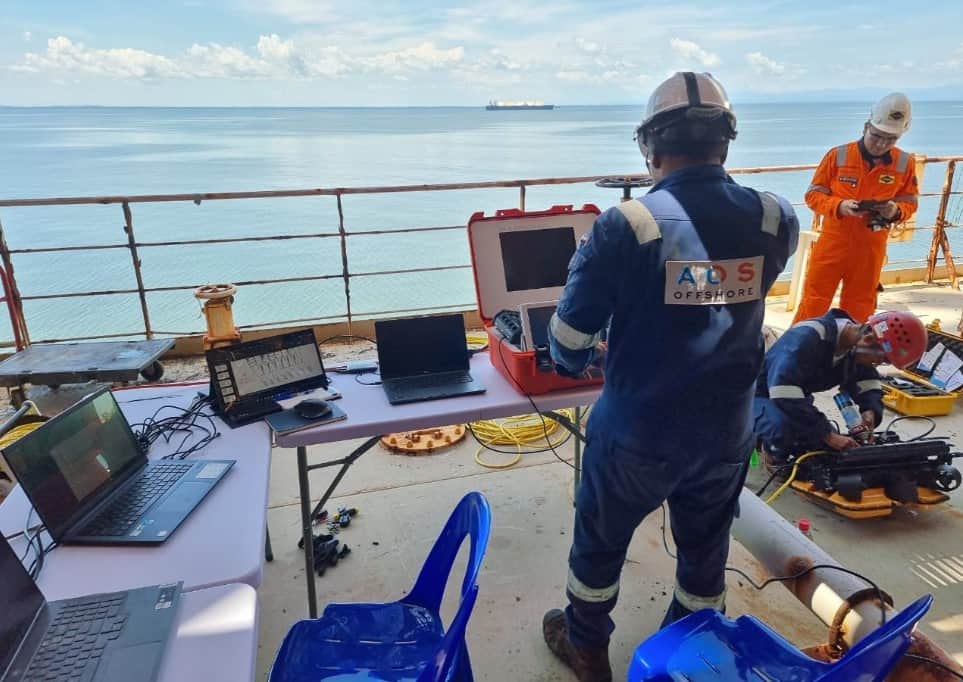
“Inspection Robot HQ” on the cargo deck is well ventilated and has a nice view.
Visual inspection with a drone
Class surveys for offshore vessels are different than for maritime vessels since the full 5-year classification scope normally is divided into yearly campaigns that ensure continuous operation of the vessel. Scopes for each inspection are different, but full coverage is required for every 5-year cycle. A work pack is created in preparation for the inspection. This describes all the inspection work to be done and how it must be done. This is often the responsibility of the inspection company, in collaboration with the class surveyor.
Flight patterns are thoroughly described and expected to be followed as closely as possible as an insurance of optimal coverage. Maps are provided, showing survey flight patterns over vessel layout plans.
For example, the tank deck is normally flown in a zig-zag pattern with the camera tilted upwards so that the entire tank deck underside can be inspected. Stringer levels are normally circled level by level since some details of the level structures can be covered manually. Such footage can be captured using handheld units like cameras and phones.
The work pack also describes which anomalies to expect and how to proceed if anomalies are found.
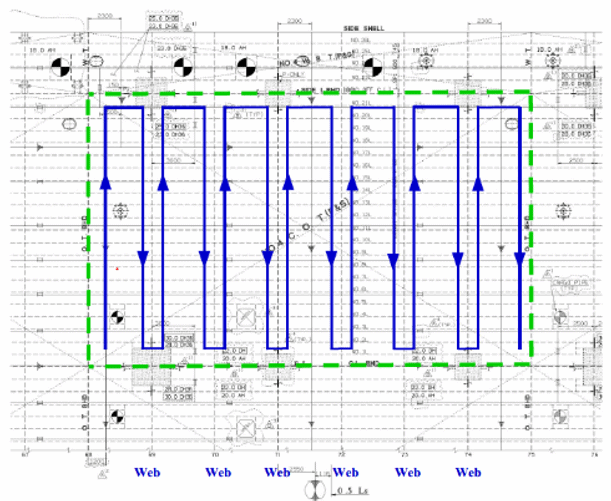
Flight plan example for under deck area of cargo tank. The green stapled lines represent the cargo tank boundary, while the blue pattern is the planned flight path.
The surveyor must approve the work pack before the inspection work can start. There is a lot of communication between surveyor, inspection company and asset operator in every case. Planning also involves finding the right time to conduct inspections.
The vessel must be available and prepared for inspection, the surveyor must be available and able to enter the vessel and so on. It is a long process involving lots of highly-trained personnel with busy schedules. And many work hours.
But preparing the inspection well pays off later. Roughly speaking, what remains after the inspection is to:
- Verify that the inspection was performed in accordance with the work pack, i.e.:
- Verify that all flight patterns were followed
- Verify that all parts of the structure were inspected
- Verify that all POI (Points of Interest) were duly recorded and marked for later scrutiny when the surveyor assesses the collected data
- To assess all the data and determine the state of the vessel.
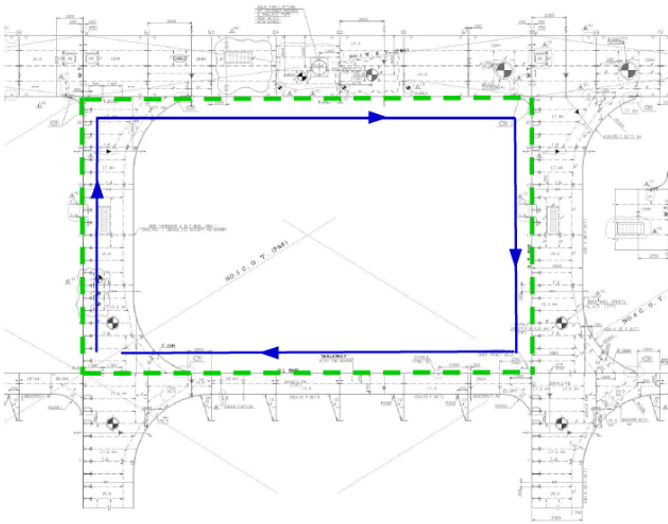
Below deck area, it is sufficient to fly along the circumference of the cargo tank wall at each stringer level.
Traditionally, the main reason for class surveyors to be onboard the vessel during inspection is to check that the job is being performed as planned. Approving the vessel is a matter of confirming whether the collected data has evidence of anomalies that need attention. This happens after the actual inspection.
The Scout 137 Drone System is equipped with a 3D LiDAR. All visual data is location-tagged, and the recorded flight pattern can be reviewed in the Scout Portal along with the visual data (see screenshot below).
Establishing work pack compliance can then be done by comparing the recorded flight patterns with the descriptions in the work pack. The flight pattern of the entire session can be viewed at any instant in the video timeline, it’s not necessary to watch the entire video feed for this purpose.
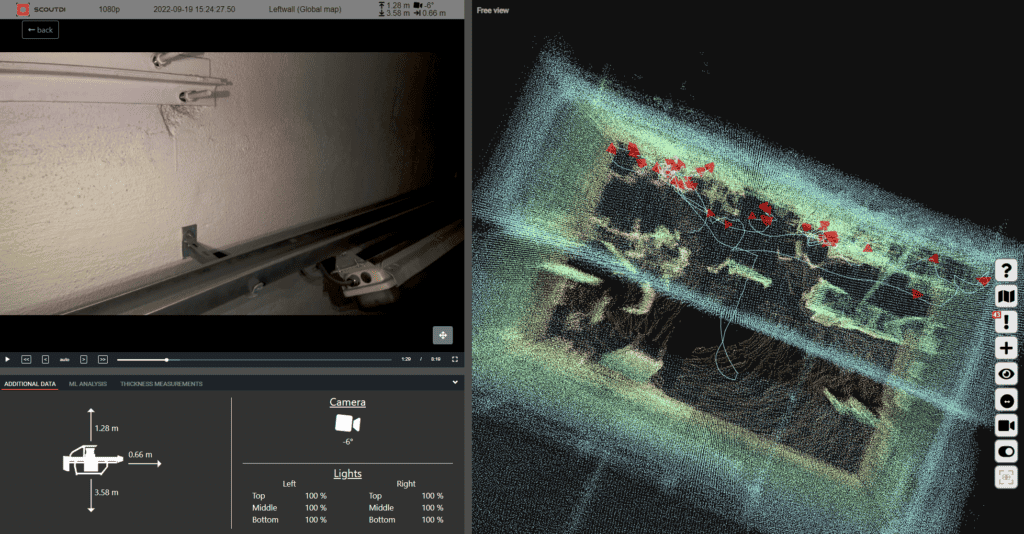
The drone’s flight path can be easily confirmed in the inspection view of the Scout Portal. The flight pattern of the entire session can be viewed at any instant in the video timeline. The red triangles are POIs. This example is from an inspection in a test facility at ScoutDI headquarters in Trondheim, Norway.
For future inspections, class may therefore choose to not to come onboard at all, but may replay the inspection in the Scout Portal, without leaving the office. The surveyor can approve flight patterns via the Scout Portal first, then decide whether to continue with examining the video and photos.
This approach saves time, provides more flexibility, and allows inspections to take place at more optimal times, with less manned entry.
All inspection data in one place and universally accessible
We’ve discussed how the Scout Portal enables new ways to organize the classification survey. Another important aspect is this: You can use the Scout Portal to store and organize videos from any 3rd party source, in addition to data collected using the Scout 137 Drone System.
While live streaming to the Scout Portal is currently limited to the Scout 137 Drone, visual data from any device can be uploaded in post and added to the inspection’s data collection. You can upload data from outdoor drones, ROVs, handheld cameras, mobile phones and any sources that can make .mov and .mp4 files.
After uploading, video files are presented as sessions under the same inspection project, organized according to site, target and inspection. You can assess all the data associated with the same inspection job via a single, globally accessible browser-based interface.
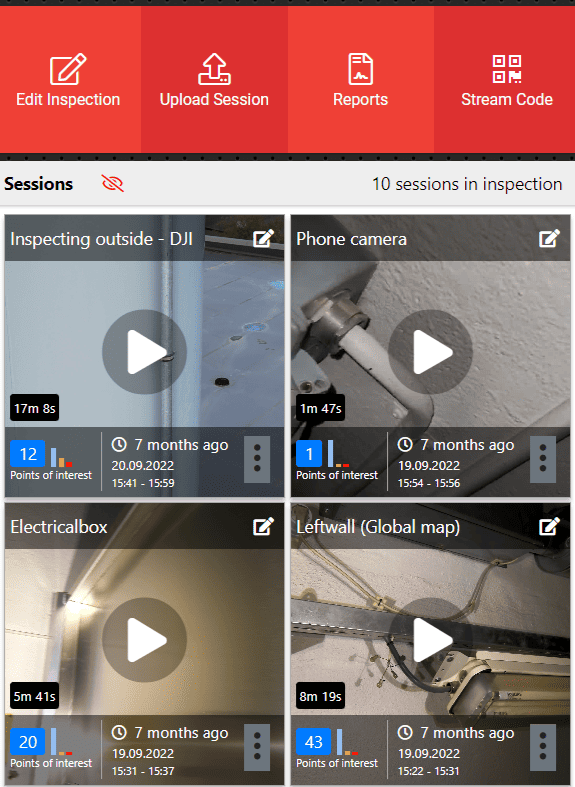
Three sources of data are all available as “sessions” under the same inspection dataset in this demo in the Scout Portal: Scout 137 drone, DJI outdoor drone and a mobile phone camera.
Click for quick video intro to the Scout Portal: https://www.scoutdi.com/scout-portal#video
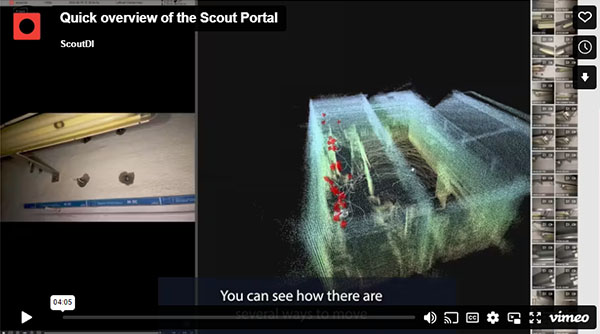
Water ballast tanks inspection
As mentioned, this was a comprehensive inspection project where several methods were used to collect visual data from several targets: Cargo tanks, water ballast tanks (WBT) and hull outside.
WBTs are deep, nested structures with little or no ambient light and limited access from the outside. One compartment provides access to the next via narrow passageways and ladders. Moving around quickly is not easy and getting out in a hurry can be a challenge. In case of any emergency, a rescue team must stand by during human entry.
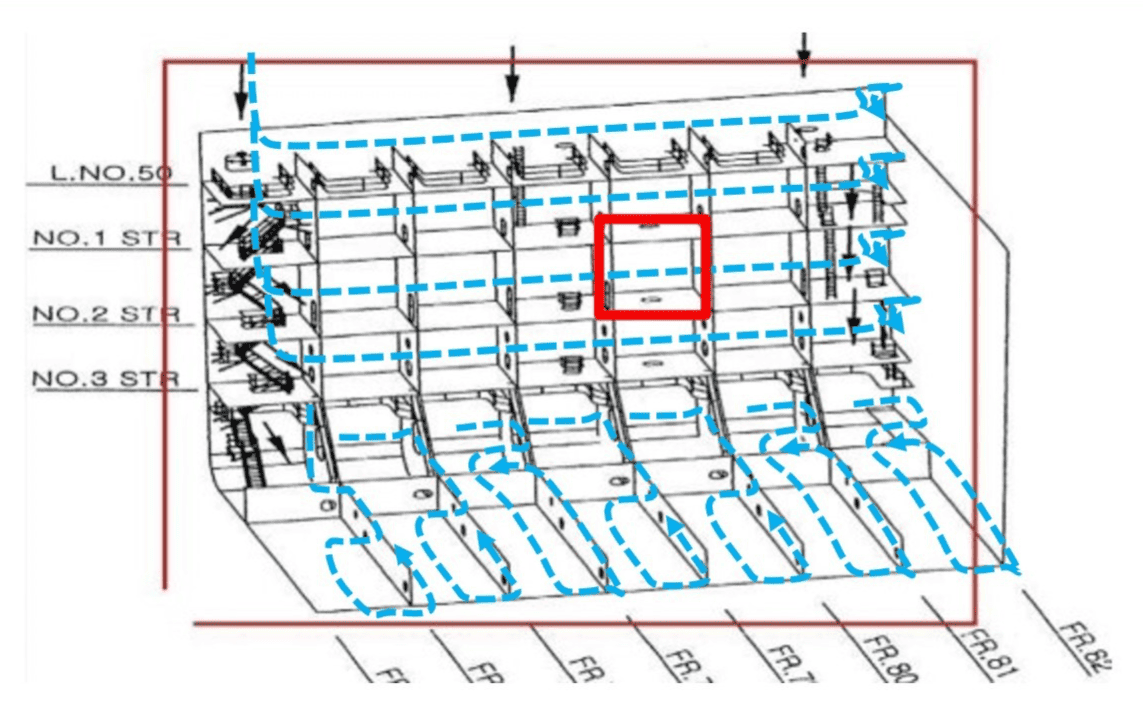
Tank entry plan for the WBT inspection by ROV. One-point entry and exit, room-to-room, wall-per-wall sweep.
Rope access is a common “traditional” method for WBT inspection. Humans enter the compartments, using handheld cameras for visual documentation. A good part of each compartment can be covered “on foot”. But on larger vessels, compartments will be tall enough that ropes or ladders are required to reach the highest areas. Most often, data coverage will consist of photos of anomalies only. Of course, emptying the WBT (“de-ballasting”) is a requirement for human entry.
It is easy to see how demands on time, planning and workforce are piling up. As are potential safety issues. For the vessel in this case study, de-ballasting alone took 5 people 9 days to complete. Then you must have planned and timed the arrival of the rope inspection crew and a surveyor, who will spend another 5 days or so inside dangerous confined spaces.
In the case of this inspection, the vessel was parked at a buoy and cargo tanks emptied. The WBT were therefore full of water and could be inspected using an ROV.
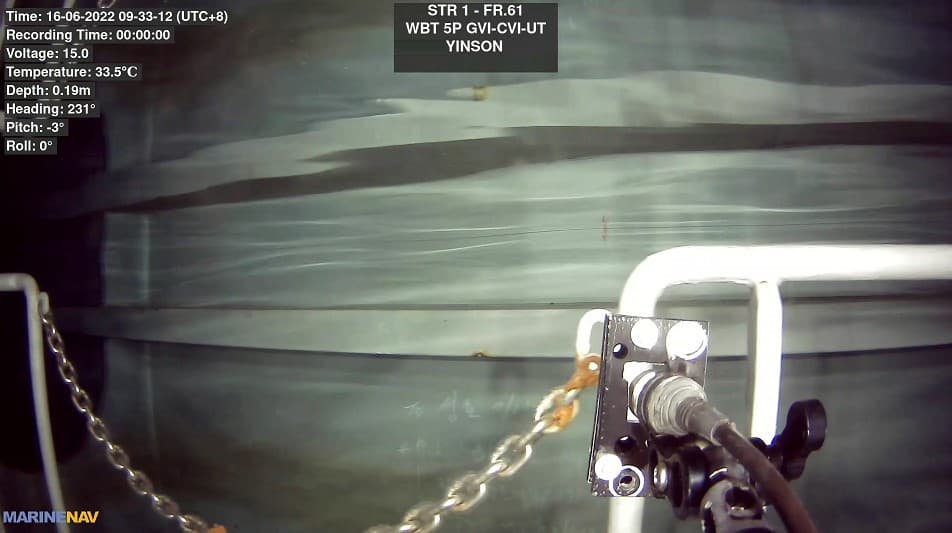
Below deck area, it is sufficient to fly along the circumference of the cargo tank wall at each stringer level.
AOS Offshore has recently also performed inspection of empty WBT using the Scout 137 Drone System. But when WBTs are empty, cargo tanks normally have cargo and cannot be inspected. So, having empty cargo tanks and filled WBT was an optimal situation in terms of inspecting as many tanks as possible in one visit.
This illustrates the flexibility available to inspection companies using both ROVs and drone systems.
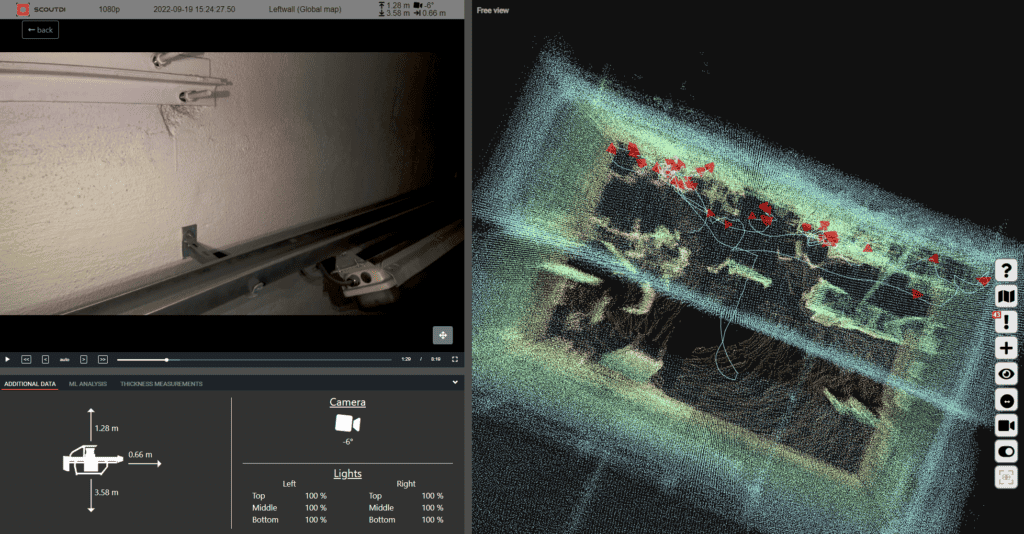
FPV video frame from ROV inspection of WBT.
AOS Offshore has recently also performed inspection of empty WBT using the Scout 137 Drone System. But when WBTs are empty, cargo tanks normally have cargo and cannot be inspected. So, having empty cargo tanks and filled WBT was an optimal situation in terms of inspecting as many tanks as possible in one visit.
This illustrates the flexibility available to inspection companies using both ROVs and drone systems.
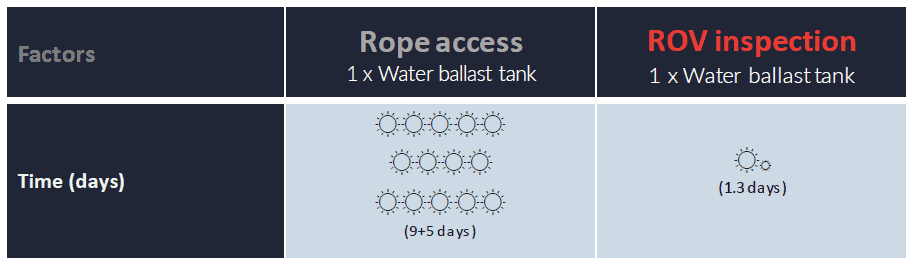
These numbers, courtesy of Yinson, show the time spent for rope access vs. ROV inspection methods. Numbers are for one water ballast tank (WBT).
The ROV inspection demonstrated similar savings to the drone inspection in terms of time. And of course, safety, since the operation required no human entry but was done via remote control.
In addition, it was also here observed that physical attendance by a surveyor was not necessary.
Just like flying a drone to inspect an empty cargo tank, the ROV in a water-filled ballast tank represents a case where a robot can take the part of a human and access the entire volume. The two cases are also similar in coverage and data quality, both providing 100% coverage and high-quality video footage.
Summary: Changing the periodic system
This case study highlighted many favorable aspects of using robots for structural integrity inspections. The main challenges stretch across many axes, including safety, cost of time and money, workforce and operational agility.
Some main challenges:
- Confined space entry
- Rope access or scaffolding
- Work at heights
- De-ballasting of Water Ballast Tank
- Use of divers for hull-side inspection (not discussed here)
- Planning overhead and process latency
- Inspection coverage and data availability
The main motivation for using modern methods is safety. Using ROVs, drones and other robots for inspection keeps people out of dangerous confined spaces and away from working at heights. In this project, all crew members remained safe on railed stringer levels or entirely outside of the volumes being inspected, with plentiful access to fresh air.
The economic aspects are short-term and long-term. The data in the table below is courtesy of Yinson, showing the amount of time saved inspecting one (1) cargo oil tank with a drone instead of using rope inspection. It is evident that there is a substantial time saving involved with drone inspection, in terms of asset down-time and man hours.
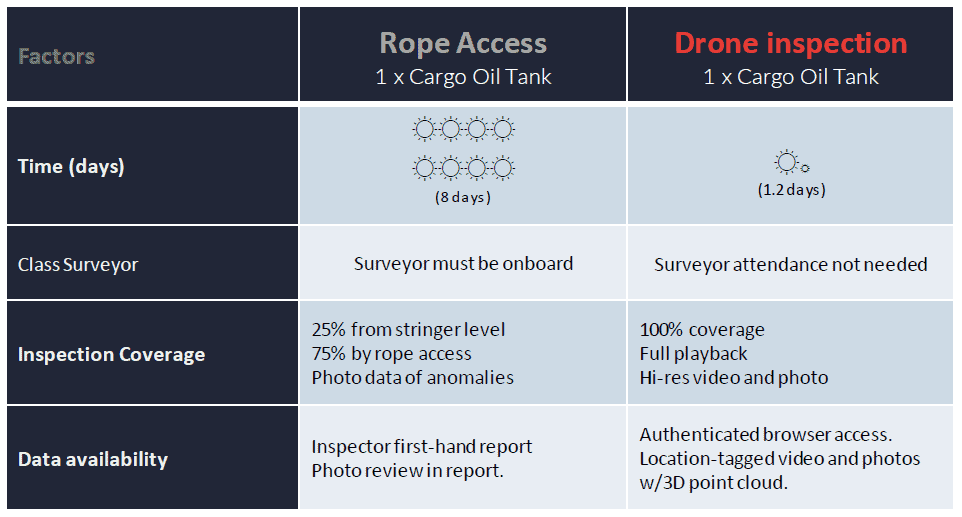
Overview of time savings with additional comments on coverage and data availability. Numbers are courtesy of Yinson and are valid for inspection of one (1) Cargo tank.
Involving smaller teams also results in less planning and travel. This has an economic impact and can be considered an environmental factor.
100% video coverage is the standard using modern methods with ROVs and drones. The robots can maintain steady motion and framing for capturing high-quality video footage, while also bringing ample light. With rope access, photos are secured for evident anomalies only, something which demands constant attention while the climber is also maintaining his personal safety. Robots allow dedicated focus on acquisition of data for later assessment.
Using ROVs and drones improves operational agility and general efficiency of the entire inspection regime. Inspections can be performed more “reactively” and with quicker turnaround instead of ruled by periodical schemes. See something unusual? Get the drone, capture data and send it to the expert for assessment.
When physical attendance by key personnel is less required, class societies may free up time for the parts of the classification work that is most relevant to their expertise. Inspection companies can operate with smaller teams and allocate them with shorter overhead.
New inspection technology has the power to lower the threshold for going out and getting important data. More frequent sampling allows earlier detection and improved prediction. Additional digital technologies, already available via the Scout Portal, allow automatic anomaly detection and comparative analysis of same structures over time.
Long-term, a safer and better maintained fleet is within reach.
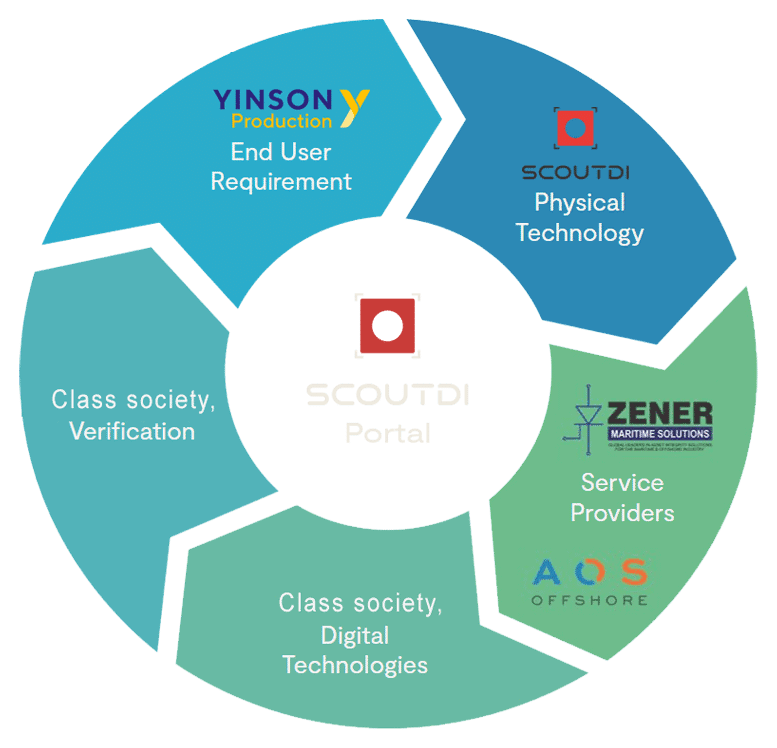
This project represents a good example of end-users, technology providers, inspection companies and class societies joining forces to explore new opportunities together. The inspection ecosystem becomes more efficient and responsive as we connect to co-develop and reiterate procedures and technology.
To all involved, thank you! 👍
Would you like to know more about the Scout 137 Drone System?
Are you looking for drone-based inspection technology for confined industrial spaces? Submit the form below to get in touch with us and we'll help you look at your options 👍
Learn More
Scout 137 Drone →
The Scout 137 Drone System has been specifically designed to give you control, coverage, and situational awareness for your confined space inspection activities.
Scout Portal →
The Scout Portal is our powerful cloud-based tool for inspection data management, review, analysis and reporting.